Okinawa: Traditional Bashofu Cloth Carries On; Fabric Made from Banana-Like Plants
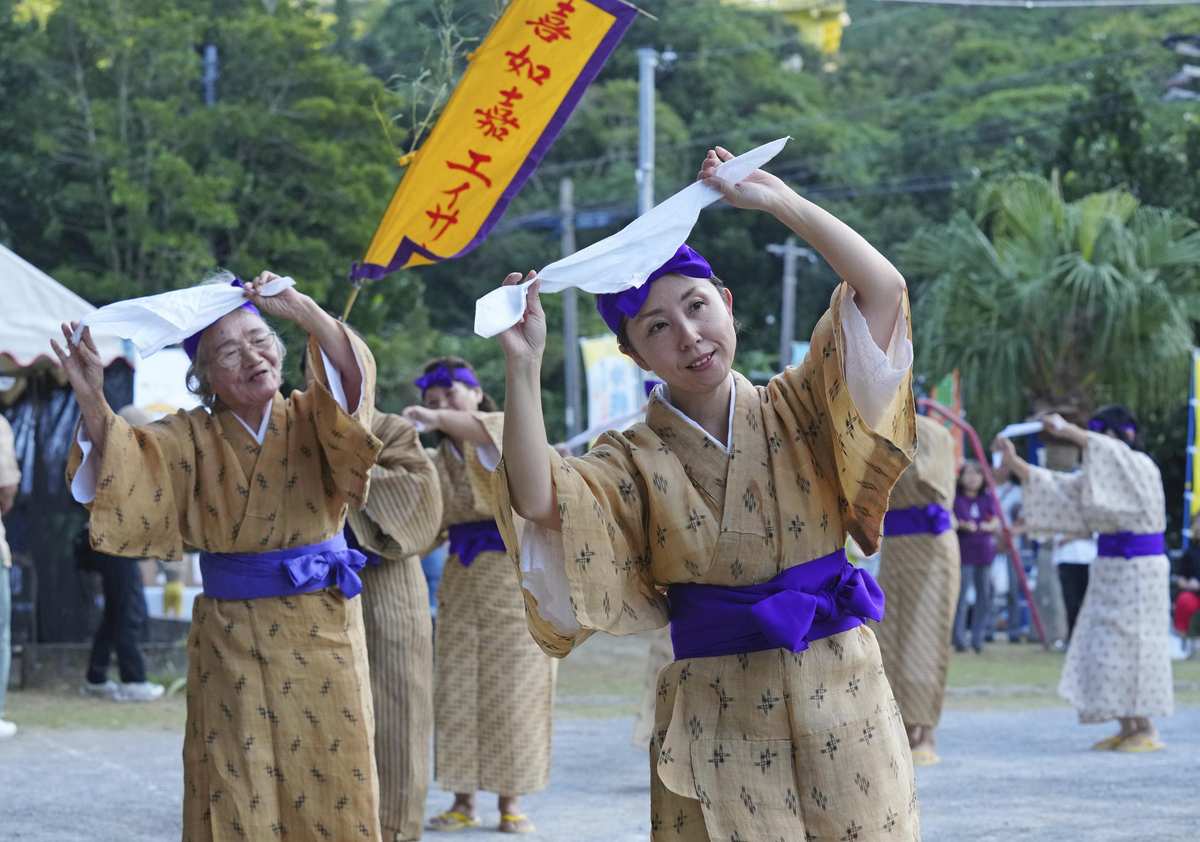
Women clad in bashofu clothes perform a dance during the Kijoka Matsuri festival, which is held biennially in Ogimi, Okinawa Prefecture, on Oct. 29, 2023.
11:01 JST, January 11, 2025
OGIMI, Okinawa — As light as a dragonfly’s wing, Okinawan traditional clothes have a unique texture that keeps the wearer cool even in hot and humid climates.

Kijoka no bashofu is a traditional fabric from the Kijoka district of Ogimi, a village in the northwest of Okinawa Island. Bashofu is woven using thread made from the fibers of itobasho, a relative of the banana plant.
As a specialty product of the Ryukyu Kingdom (1429-1872), the clothes were given as tribute to the Tokugawa shogunate and China’s Qing dynasty. In the 1930s, leaps were made in developing the fabric’s manufacturing, resulting in improved quality and productivity.
However, production began to wane in the wake of the Battle of Okinawa during World War II. The U.S. military cut down the itobasho plants to prevent malaria-carrying mosquitoes from breeding, and the tradition was in danger of disappearing.
Toshiko Taira (1921-2022), a native of the Kijoka district, and other locals made efforts to revive production of the fabric. Taira was in Kurashiki, Okayama Prefecture, when the war ended. Having gone there to study textile fabrics, she returned to the village in 1946 and began cultivating farmland to grow itobasho and reconnect with the tradition, which was in disarray. She later became a living national treasure.
Complicated process
Production of bashofu is divided into many steps, which are completed by around 80 workers.

A craftsman peels the skins of itobasho plants, which are used to make fibers for cloth.
The peak harvest season of itobasho is between October and February. Workers cut down the plants, which are grown for three years and stand as tall as a human, and strip off the skin, which is used to make the fiber. About 200 plants are needed to make one kimono.
The plant skins are then boiled in alkaline wood lye, and unnecessary scraps are removed from the surface. However, each thread obtained from the skins is less than one meter long. To make it longer, several threads have to be tied together.
About 22,000 short threads need to be tied together to make enough for one kimono. The process requires a high degree of skill.

Fibers of itobasho skin are tied to make longer threads.

Yellow- and red-dyed itobasho thread
The strings are then twisted to increase their strength. Following that, they are dyed.
Only natural dyes are used: Ryukyu indigo for blue and navy blue, fukugi tree for bright yellow and Indian madder for red. For green, considered a noble color in the area, the threads are initially dyed with fukugi and then dyed again with indigo.
Itobasho thread is vulnerable to dryness. For the finishing weave, humidifiers are used to keep the humidity inside the weaving room at 80% or higher. And during the process, misters are used to spray the threads with water.
In studios where silk and cotton clothes are woven, a fast and rhythmic sound is generally heard from the weaving machines. In contrast, the studios that produce bashofu clothes are quiet. The fabrics are woven very carefully so that the threads do not break. If they do, spare thread is used to retie them.
It takes about a month to weave one kimono’s worth of fabric, though the length of the time differs depending on the weavers’ skills and the patterns on the clothes.
Additional work is done after that, and then the durable, high-quality bashofu clothes are complete.

Craftswomen weave bashofu with weaving machines.
Difficulty in relaying
Kijoka no bashofu cloth was designated as an important national intangible cultural property in 1974, and a society to preserve the product was established that year.
The society currently has 11 members chosen from among highly skilled craftspeople. Though the society is trying to foster successors, the number of craftspeople, especially those in charge of tying the threads, has been decreasing. The society faces difficulty in relaying the skills to the next generation.
But the interest surrounding bashofu is high. When the Okinawa Prefectural Museum and Art Museum in Naha held an exhibition of bashofu clothes from Oct. 1 to Dec. 1, the number of visitors was double those at other exhibitions.
When a noh performance focusing on bashofu clothes was held in the Kijoka district on Nov. 14, more than 400 people were in attendance.
“I hope these kinds of events will increase and more people will know how good bashofu clothes are,” said Mieiko Taira, 76, head of the Bashofu Preservation Society of Kijoka.
"Features" POPULAR ARTICLE
-
Ueno Park Cherry Blossoms in Full Bloom in Tokyo; About 800 Trees Present ‘Overwhelming Beauty’
-
Cherry Blossoms in Full Glory at Japan’s Takato Castle Park; Deep Red Flowers Blooming on About 1,500 Trees
-
‘Cherry Blossom Tunnel’ Opens at Osaka Mint Bureau
-
Osaka: Japan’s Longest Pedestrian Suspension Bridge Opens; Structure Spans 420 Meters over Lake
-
Japan’s Miyagi Pref.’s Cherry Blossom Trees in Peak Bloom; Trains Reduce Speeds While Moving Along Line of Flowering Trees
JN ACCESS RANKING