More Japanese Timber Being Used to Build Shops, Other Buildings
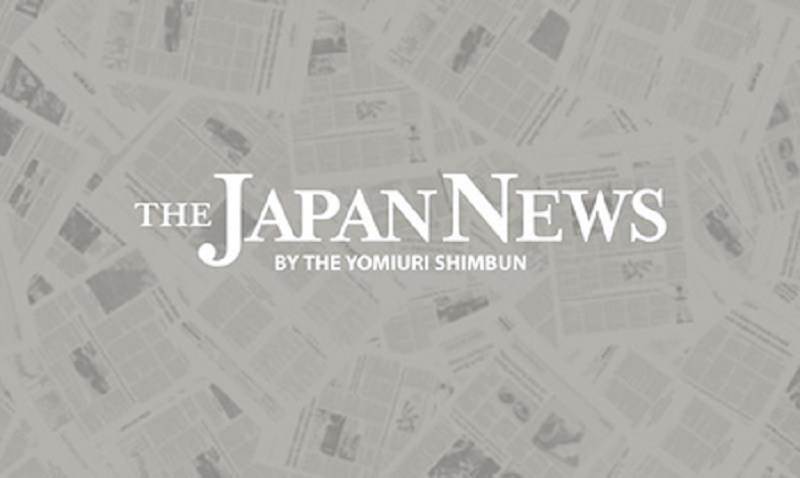
17:54 JST, January 5, 2021
The use of domestic timber, such as sugi cedar and hinoki cypress, is gaining momentum in the construction of shops and other buildings, and it’s seen as a plus in the effort to reduce greenhouse gas emissions, because trees absorb CO2 as they grow.
Despite being in line with recent government pronouncements on decarbonization, there are still the usual hurdles when building with wood, such as additional costs to ensure fire resistance.
■ Improving fire resistance
Mitsui Fudosan Co. and Takenaka Corp. are planning to erect a 17-story structure in the Nihonbashi quarter of Chuo Ward, Tokyo, that is set to become Japan’s tallest wooden building at about 70 meters in height. The companies will use more than 1,000 cubic meters of mostly domestic wood, making it largest-scale project of this kind in the country. Construction is scheduled to start in 2023 and be completed in 2025.
Materials that are hard to burn, such as mortar and plaster, will be incorporated in the building’s wooden pillars and beams to make them fireproof for up to two hours of exposure to flames. Based on the Building Standard Law, the 4th to 17th floors of a 17-story building can be built of wood with two hours of fire resistance.
In November last year, Seven-Eleven Japan Co. opened a shop built of wood in Ome, western Tokyo, using domestic timber for pillars and beams. The company will increase the number of such shops to about 15 by February.
McDonald’s Company (Japan), Ltd., has also used domestic timber for pillars and other parts of its restaurants, and has built seven restaurants out of wood — mostly one-story buildings — since 2019. Wood is also used in the interiors and exteriors of about 50 McDonald restaurants in Japan.
■ Recovering self-sufficiency rate
In Japan, a large amount of sugi cedar and hinoki cypress trees were planted after World War II to meet the rising housing demand. However, domestic timber consumption gradually declined as the use of steel and concrete increased alongside expanded imports of inexpensive timber from overseas, mainly Southeast Asia. Against this backdrop, the self-sufficiency rate of timber in Japan had fallen to 18.8% by 2002.
In recent years, Southeast Asian and other countries have restricted exports of raw wood one after another over fears of the depletion of resources. This saw the self-sufficiency rate of wood in Japan recover to 37.8% in 2019.
According to the Forestry Agency, wood is regaining recognition as a building material because the amount of greenhouse gas emissions for a wooden house is about 40% less than that of a building made of concrete or other materials.
■ Cost considerations
Wooden structures generally cost less to build than concrete ones and provide better conditions for the control of humidity, offering inhabitants a more comfortable environment. In order to put them on par with concrete buildings for fire resistance, mortar and other fireproofing materials need to be incorporated. And this tends to raise the costs of wooden buildings.
A survey by Keizai Doyukai (Japan Association of Corporate Executives) published in 2018 that received responses from 56 companies posed the question of what is necessary when considering the construction of buildings with wood. The answer given by the largest number of the respondents, at 43%, was “explanations on the advantage [of a wooden building] that makes up for the high cost.” “Technical explanations on fire resistance, earthquake resistance, durability et al” was indicated by 33% of the respondents.
These answers highlighted their concern over the performance and cost of a wooden building.
"Society" POPULAR ARTICLE
-
World War II Battleship Yamato Was Outdated From the Start; Unable to Compete With Newly Developed Warplanes
-
Nankai Trough Megaquake Estimated Death Toll Lowered, Tsunami-hit Area Increased in Govt Report
-
Cherry Blossoms Reach Full Bloom in Tokyo; Ueno Park Draws Many Viewers
-
Cherry Blossoms Officially in Bloom in Tokyo, Beating Last Year’s Date by 5 Days
-
2025 Expo Osaka: Tokyo Police on High Alert Ahead of Opening; Officials Cautious over Possibility of Lone Offenders, Cyberattacks
JN ACCESS RANKING