An aircraft carrier slowly takes shape, hundreds of tons at a time
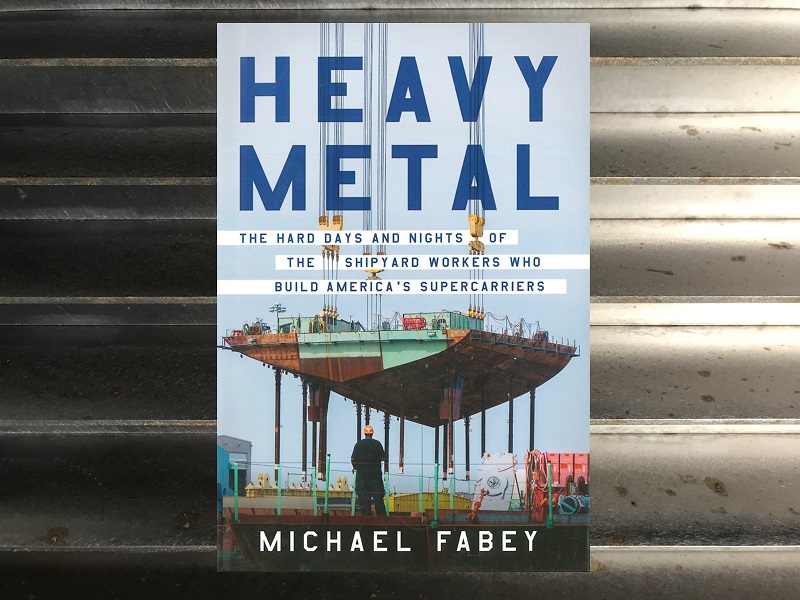
15:19 JST, October 9, 2022
Heavy Metal: The Hard Days and Nights of the Shipyard Workers who Build America’s Supercarriers
By Michael Fabey
William Morrow, 306pp, $28.99
Rome wasn’t built in a day. Building an aircraft carrier, often described as a floating city, is no afternoon project either.
U.S. Navy carriers, including the Yokosuka-based Ronald Reagan, are constructed at Newport News Shipbuilding, where the James River empties into Chesapeake Bay on the Atlantic coast of Virginia. Military affairs journalist Michael Fabey walks readers through the yard’s carrier-building process in his fact-filled book “Heavy Metal.”
The Reagan is a nuclear-powered Nimitz-class carrier. “Heavy Metal” focuses mainly on the new Ford class, named for its first ship, the Gerald R. Ford, which features an array of technological upgrades.
Perhaps the most amazing of these involves a carrier’s core function: launching planes.
On a Nimitz carrier, a blast of steam from the nuclear reactors shoots a metal slug (“like a popped champagne cork,” Fabey writes) along the length of the ship, under the top deck. The slug is attached to a shuttle above deck, and the front wheels of an airplane are attached to the shuttle. And off it goes.
The speeding slug has to be stopped before it, too, shoots right off the ship. This is achieved with a “water brake” that uses nearly 5,000 liters per minute.
The Ford ships do away with steam in favor of the lighter and less bulky electromagnetic aircraft launch system (EMALS). Basically “linear induction motors along a metal track,” EMALS has fewer moving parts, requires fewer personnel to operate, can launch planes at a faster rate, and can be precisely computer-adjusted for a wide variety of lighter or heavier aircraft, including drones.
Fabey traces the lengthy process of building the second Ford ship, the John F. Kennedy, for which the first steel was cut in 2011 and whose keel was laid in 2015. After that, the ship was built “from the bottom up and the middle out,” using a crane to position hundreds of prefabricated sections called lifts, including “superlifts” of up to 900 tons. The most dramatic lift is the island (which landlubbers might call the control tower), which gave the carrier its distinctive final shape in May of 2019.
In December of that year, former U.S. Ambassador to Japan Caroline Kennedy christened the ship with a bottle of champagne, just as she had done at the same shipyard in 1967 at the age of 9, for an earlier carrier also named after her father.
Even with a splash of bubbly on its bow, the ship was not yet finished. There was a great deal of interior work still to be done with the Kennedy afloat. The shipbuilders gradually handed over sections of the vessel to the U.S. Navy as they became ready for use.
In fact, it is not set to be fully “delivered” until 2024.
Fabey interviewed many people at many levels of the shipyard and the navy. On the last page of the book, he quotes a yard executive as remarking, “Remember this — the last commanding officer of the JFK hasn’t even been born yet, that’s how long this ship will be in service.”
From that perspective, one can see why they have taken so many years to try to build it right.
"JN Specialities" POPULAR ARTICLE
-
Walking through Japan’s Waterfall Paradise Created by Lava; Highly Carbonated Hot Springs Also Popular at Hida-Osaka in Gifu Pref.
-
Letter from New York / The Changing Face of The City: New Immigrants Are Transforming New York
-
The Japan News / Weekly Edition (7/19-7/25)
-
The Japan News / Weekly Edition (7/5-7/11)
-
The Japan News / Weekly Edition (7/12-7/18)
JN ACCESS RANKING