Infinite Combinations of Hakone-Yosegi-Zaiku Traditional Patterns
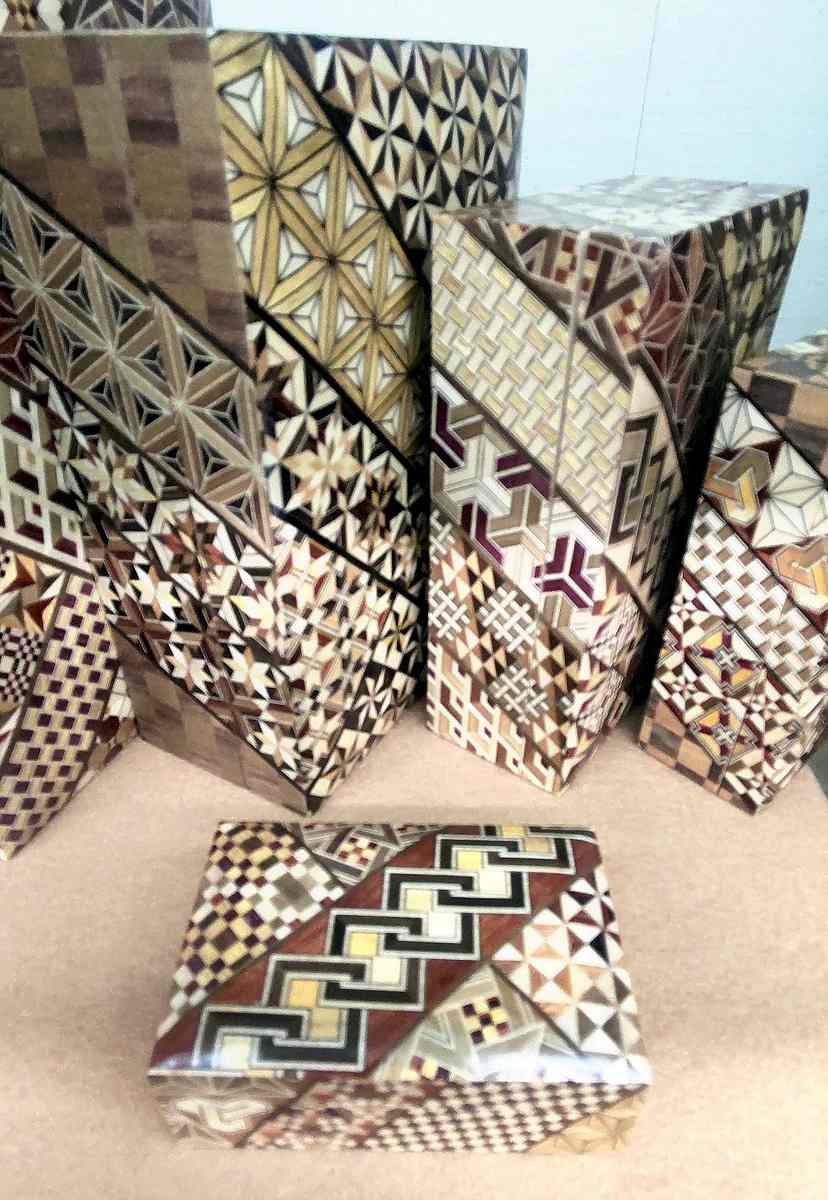
A small Hakone-Yosegi-Zaiku box with a beautiful combination of complex patterns
14:00 JST, March 24, 2024
Creating beautiful geometric patterns by combining different colored pieces of wood, Hakone-Yosegi-Zaiku is a handicraft that takes advantage of the unique characteristics of the Hakone mountain range, which has a wide variety of trees thanks to its variations in elevation. The craft is famously used as the trophy awarded to the first day’s winning team of the Tokyo-Hakone Intercollegiate Ekiden relay race.
The craft is said to have originated during the late Edo period (1603-1867) as the creation of Ishikawa Nihee in a post-station town, which is in present-day Hakone, Kanagawa Prefecture. In the original zuku-bari technique, a large tane-ita patterned board is shaved to a thickness of 0.15 to 0.2 millimeters with a plane, placed into thin sheets and pasted on small boxes, chests, trays, and other objects as a decorative material. Later, muku-zukuri, a technique of making trays and tea caddies by hollowing out tane-ita boards, was invented.
At Hamamatsuya, a manufacturer’s direct sales shop about 15 minutes by bus from Hakone-Yumoto Station, Ichiro Ishikawa, 69, the seventh-generation descendant of the founder, was making the smallest units of patterns by putting together wooden sticks that had been cut into rhombuses and triangles. Movements of hands to tie strings and a brush to apply glue were smooth and fluid.
There are about 60 traditional patterns created with these blocks, including “Ichimatsu,” “Hakkaku-Asanoha” and “Hishi-Mannji.” Work requires intense accuracy, as even the slightest misalignment can disrupt the entire pattern. It is said to take 10 years just to master basic patterns.
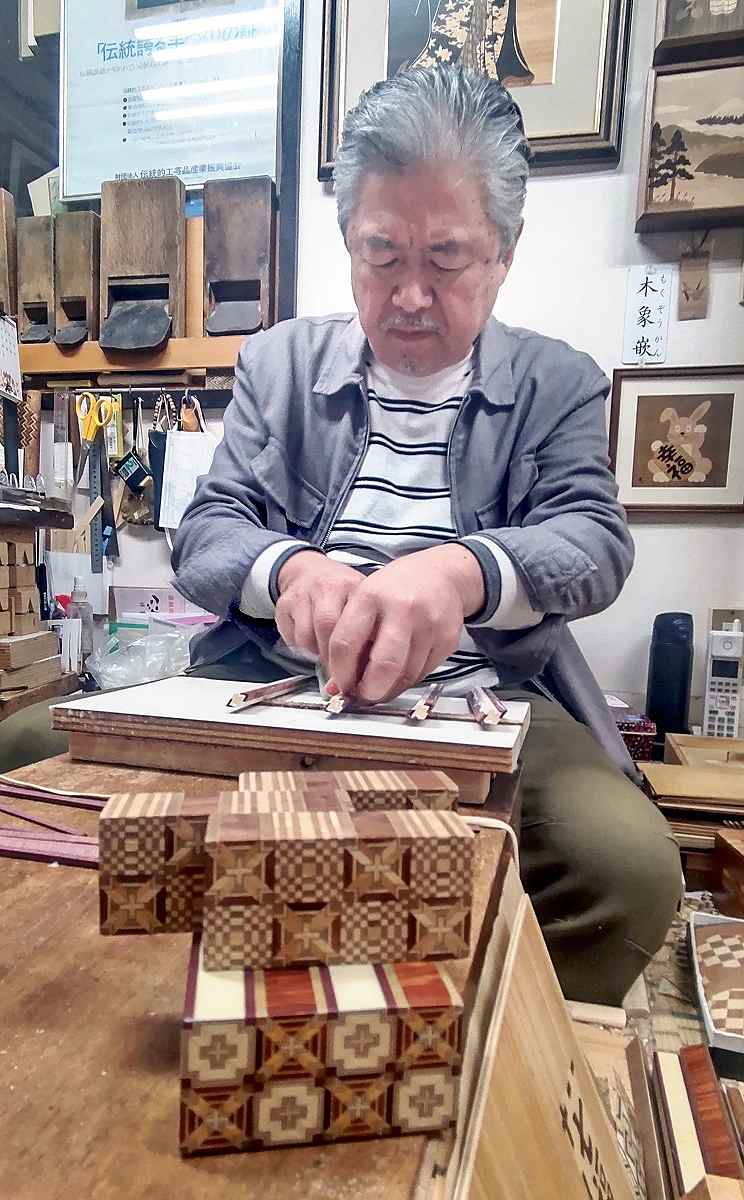
Ichiro Ishikawa puts together various types of wood to create patterns.
“It would be boring to keep making the same thing over and over,” said Ishikawa, who has more than 40 years of experience as a craftsperson. He quickly changed the color and arrangement of the pattern. The pattern then gave off a more vibrant impression. “There are infinite combinations. I like to think of more complex patterns on my own,” he said.
For a marquetry craftsperson, he says, the most important thing is to be willing to take on challenges. He believes that if they only stick to traditional techniques, their work will fall behind the times and out of use. He is actively involved in collaborative projects, weaving his work into Nishijin-ori obi sashes, applying them to smartphone cases, wallets, zori sandals, guitars and so on.
For the past 35 years or so from the time of his predecessor, the shop has been open to the public to watch the production process. “It’s best that people actually see the work and understand how things are made. Conversations with the customers are encouraging,” Ishikawa said. The number of foreign customers is also increasing. He has a feeling that he will get inspiration for a new challenge from them.
"Society" POPULAR ARTICLE
-
Japan Court OKs Sex Change without Surgery
-
3 Climbers Die On Mt. Fuji Within 2 Days Of Opening; Japan Police, Guides Urge Climbers To Prepare Well, Make Wise Decisions
-
Sex Crime Perpetrators Linked to U.S. Military in 166 Cases in Japan over 35 years; Local, Prefectural Governments Often Not Aware of Crimes
-
New Mt. Fuji Rules Reduce ‘Bullet Climbers’ by 90%; Access to Japan’s Iconic Peak Limited from Yamanashi Pref. Side
-
Tokaido Shinkansen Trains Suspended Between Hamamatsu and Nagoya Due to Accident; Resuming Services Expected Noon at Earliest
JN ACCESS RANKING