Artisan Pushes Boundaries of Koishiwara Pottery
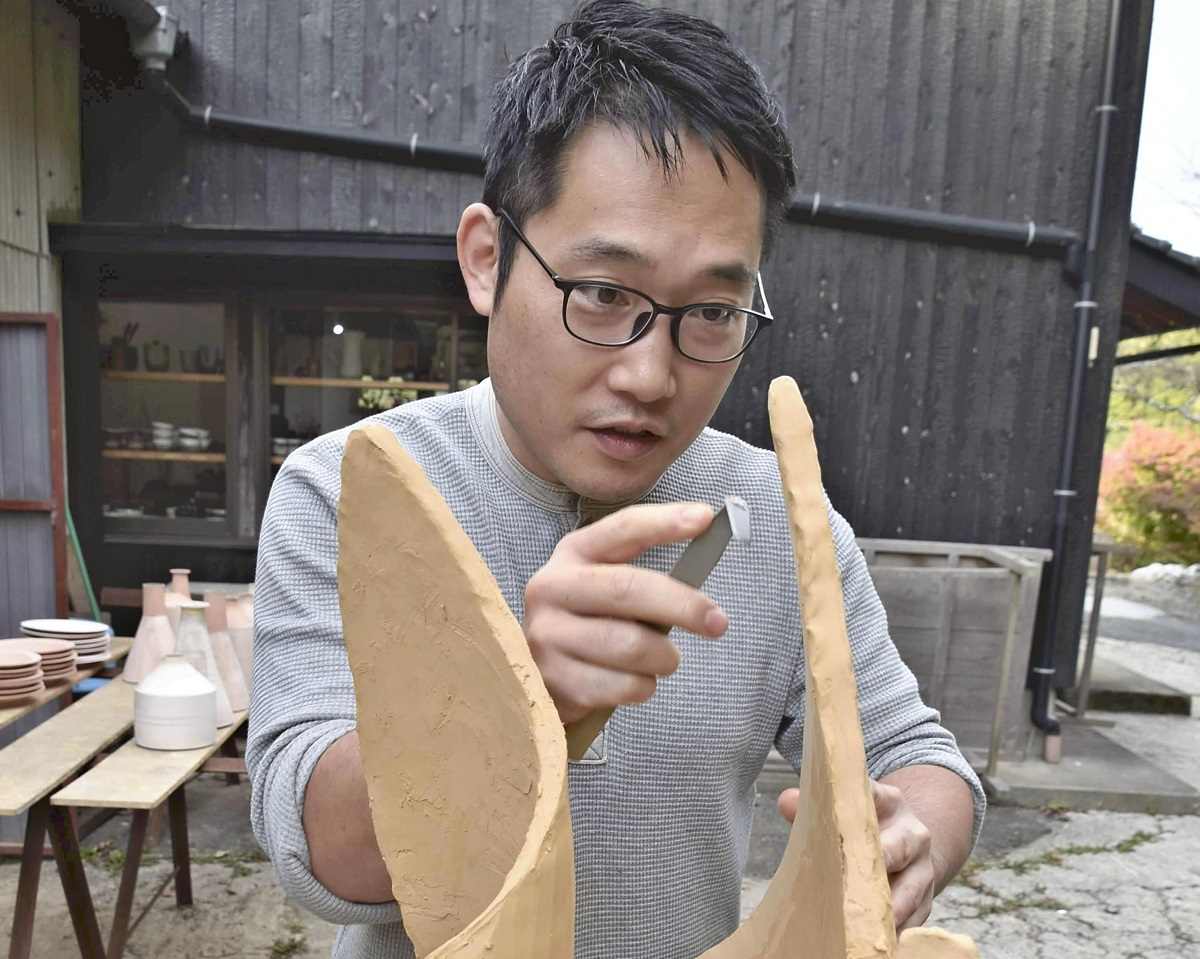
Kanjiro Moriyama uses a tool to shape an artwork.
10:00 JST, January 21, 2024
FUKUOKA — The object looked so modern that I wondered if it was really Koishiwara ware. Its intertwined parts seemed sharp and delicate, while its hard, metal-like texture imbued it with an air of quiet solemnity.
The mountain village of Toho sits in the eastern part of Fukuoka Prefecture. Here, ceramic artist Kanjiro Moriyama, 39, crafts Koishiwara pottery, which is popular as tableware and known for its earthy texture.
Koishiwara pottery dates back to 1682, when a feudal lord of Fukuoka called upon the talents of a potter from present-day Imari in Saga Prefecture.
The potter interacted with local Takatori pottery craftsmen, leading to the development of the Koishiwara pottery, which is characterized by “tobikanna,” patterns, engendered by plane shaving, and “hakeme,” a technique that involves using a brush.
Though the popularity of Koishiwara pottery temporarily declined during World War II, it was revived during the mingei folkcraft boom from the 1950s to 1980s. In 1975, Koishiwara became the first porcelain ware to be designated by the government as a traditional craft. Today, about 50 kilns produce Koishiwara pottery.
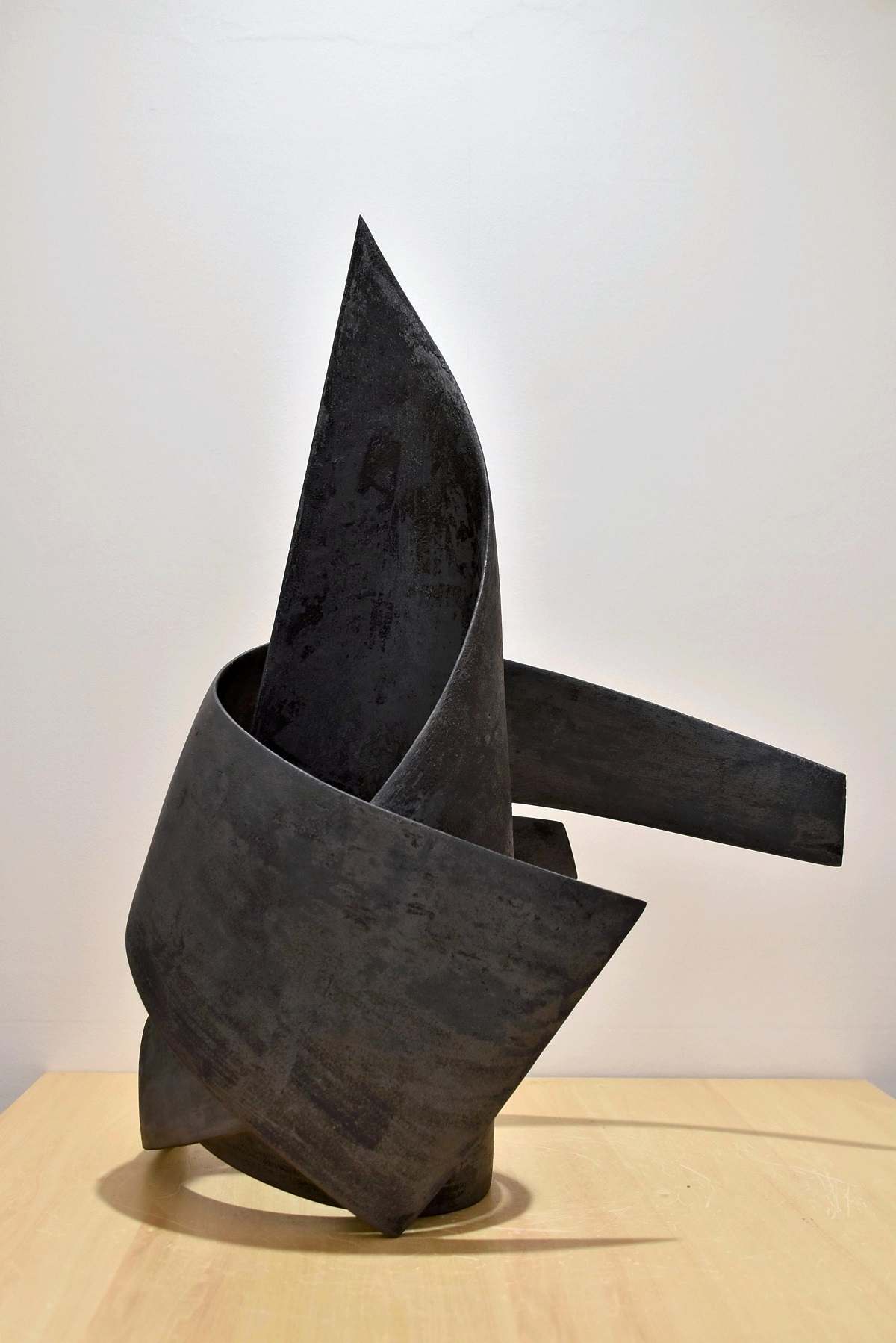
An artwork created by Kanjiro Moriyama
Initial inspiration
Moriyama was was a student at Saga Prefectural Arita Technical High School when he was first inspired by a photograph of a ceramic figurine crafted by Sueharu Fukami. “I wondered how he made it,” Moriyama recalled.
After entering Saga University, Moriyama pursued his own techniques, and in 2008, he began working at the Toho-based Kanzan Kiln, run by his father Motomi, 75.
Since then, Moriyama has poured his efforts into artistic objects for a twice-yearly pottery festival, while also creating tableware and other ceramic objects.
Moriyama uses a potter’s wheel to create cylindrical shapes, then uses string and a plane to make fine adjustments. He repeatedly glazes different parts in a kiln, joins them together using a highly viscous glaze, then bakes them again and makes final touches with resin.
Moriyama calls the technique “kiritsugi.” At first, he limited his works to items around 30 centimeters high. Now, however, he makes objects that measure up to 1 meter in height, the maximum size for his family’s kiln.
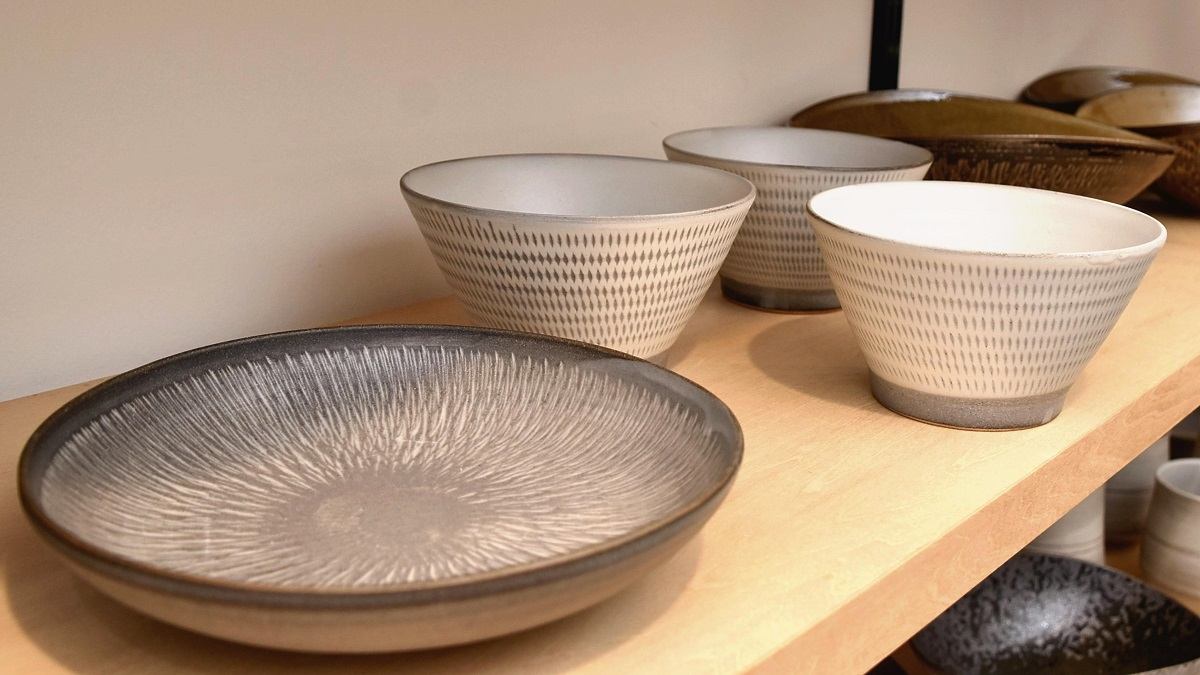
Tableware made by Kanjiro Moriyama
Living national treasure
Zenzo Fukushima, 64, is a living national treasure, a designated holder of important intangible cultural property regarding Koishiwara ware. “Koishiwara clay contains a lot of iron and glazes go well together,” Fukushima noted. “[Moriyama’s] pieces take good advantage of this characteristic.”
“The tobikanna technique came about in the early part of the Showa era (1926-1989) and has figured in the last 80 years of Koishiwara pottery’s 350-year history,” Fukushima added. “Everything starts somewhere, and new techniques that stand the test of time will become traditions.”
Presently, Moriyama strives to create Koishiwara ceramic objects by hand, without using a potter’s wheel. “Having various styles will help revitalize the production area,” he explained. “I’d like to try new things while keeping time-wrought traditions in mind.”
"Culture" POPULAR ARTICLE
-
Maison Yoshiki Makes Paris Debut During City’s Fashion Week; Yoshiki Plays Piano as Models Walk Runway Near Eiffel Tower
-
KLP48 Debuts in Malaysia, Overseas Sister Group of Beloved Japanese Pop Idol Group AKB48
-
Indonesian Artist Eko Nugroho’s Embroidered Paintings Urge for ‘More Love Above The Peace’; Pieces Explore Politics, Social Issues of Indonesia
-
More Attention Sought for Creators of Atomic Bomb Paintings; ‘Hiroshima Panels’ Exhibited Around Japan and in 20 Countries
-
Kawamura Memorial DIC Museum of Art to Close from March; Options for Downsizing or Shutting Down Being Weighed
JN ACCESS RANKING