Japanese Artist’s Wooden Mechanical Artworks Find Another Gear
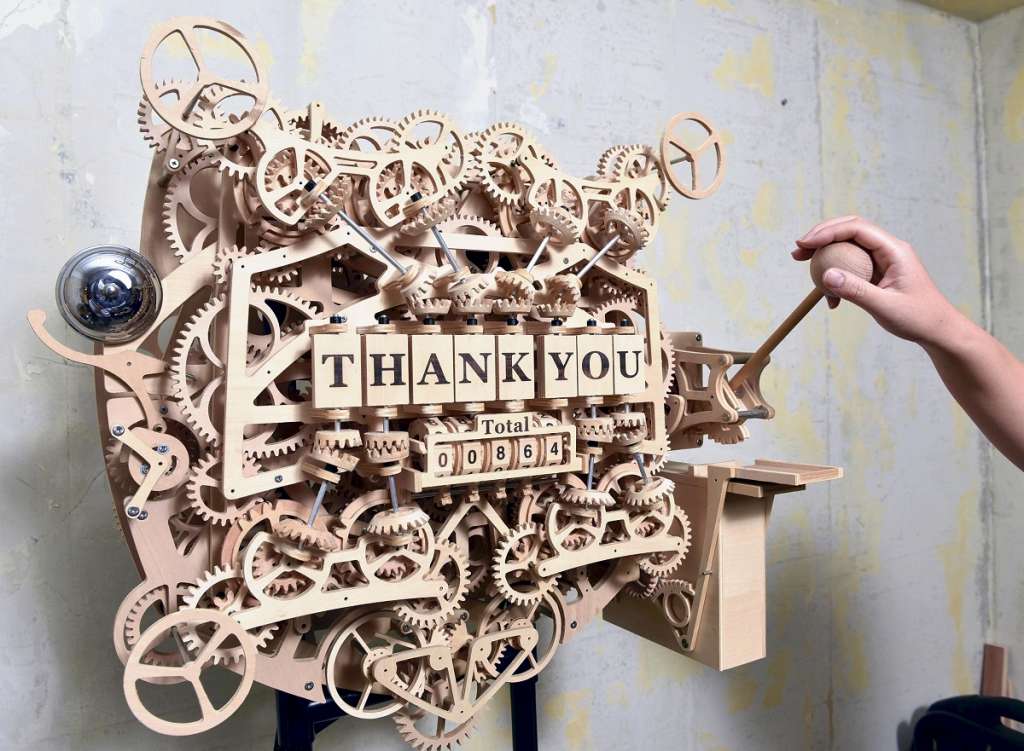
“Karakuri Kessai” comprises about 2,000 components. Collection of Book Culture Club in Kichijoji, Tokyo
12:00 JST, December 15, 2023
The dry sound of multiple wooden gears interlocking and moving within a mechanical device is pleasing to the ear, and the intricate movements are fascinating to watch.
Such intricately assembled devices are known in Japan as “karakuri.” Typically, karakuri mechanisms do not use electricity, instead relying on manually powered gears and shafts.
Pulling on a lever on the side of one such device caused the gears to engage and turn. Eight plates installed on the front of the machine flipped over in sequence, revealing a message that read “THANK YOU.”
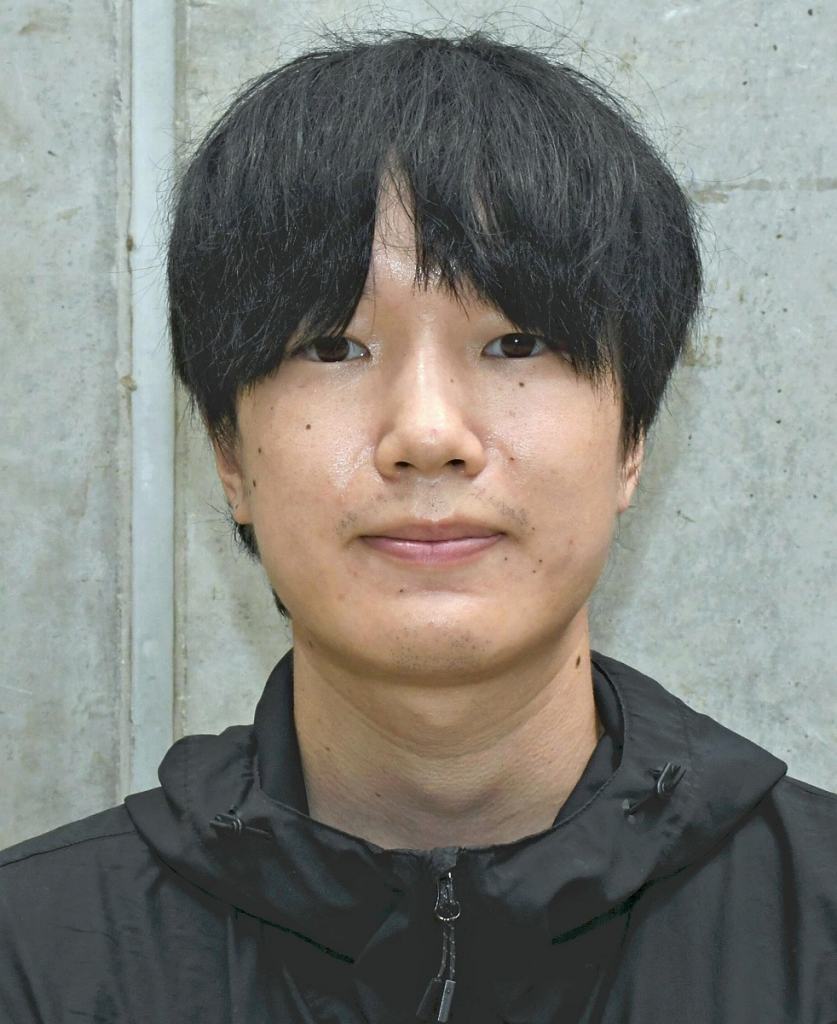
Kango Suzuki
The creation in question, “Karakuri Kessai” — literally “karakuri transaction” — was created by Kango Suzuki. Suzuki says the work, comprising about 2,000 separate parts, was inspired by a cash register. I stared in awe at the mechanism’s movements for about 30 seconds.
“These days, there are many machines that are like black boxes, which operate without us knowing what’s inside. However, [karakuri] allows people to witness the actual movements, which is very attractive,” said Suzuki, 30.
Another of Suzuki’s works “Ha to Hana no Karakuri” (Karakuri of teeth and flowers) resonates with a strong presence.
When operated, gears turn and depictions of flowers and leaves open and close. The way the “plants” move evoke a living creature.
It takes Suzuki about two to three weeks to design and create a piece. He utilizes sturdy woods such as oak and cherry, and cuts out parts using an automatically controlled machine, then manually files, greases and assembles the parts.
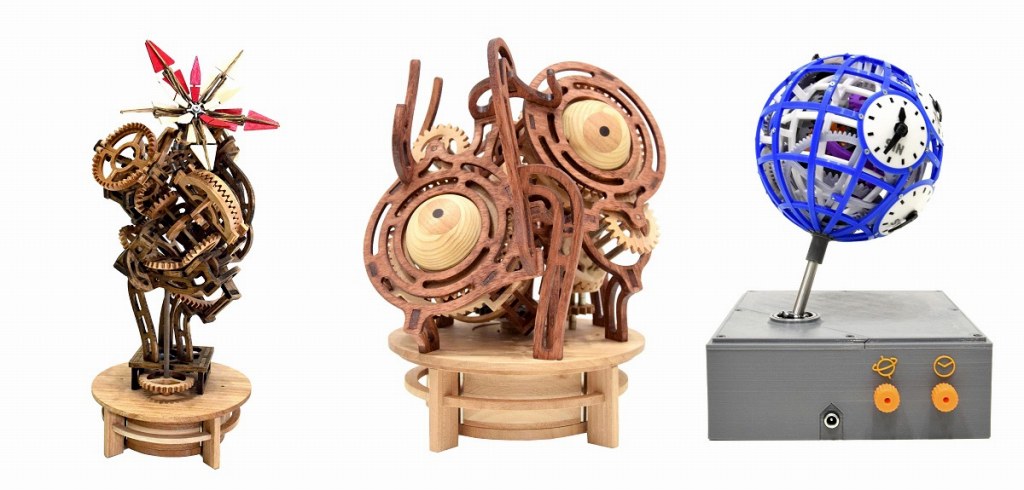
From left: “Ha to Hana no Karakuri,” “Homunculus” and “Kyutaigata Sekaidokei” was created using a 3D printer
“Sometimes the parts interfere with each other and don’t work as expected,” he said. “Redesigning the device is the hardest part.”
Some have described Suzuki’s output as “amazing.” One of his works, “Homunculus,” stirred considerable surprise, he said. “Homunculus” has two “eyes,” designed to move independently and irregularly. He made the two eyes into independent mechanisms and devised the gears to mesh with each other, he said.
About a year ago, Suzuki began using a 3D printer to create plastic works, including “Kyutaigata Sekaidokei” (Sphere-shaped world clock).
“I hope to spread the fun of manufacturing by laying bare mechanisms’ movements,” he said.
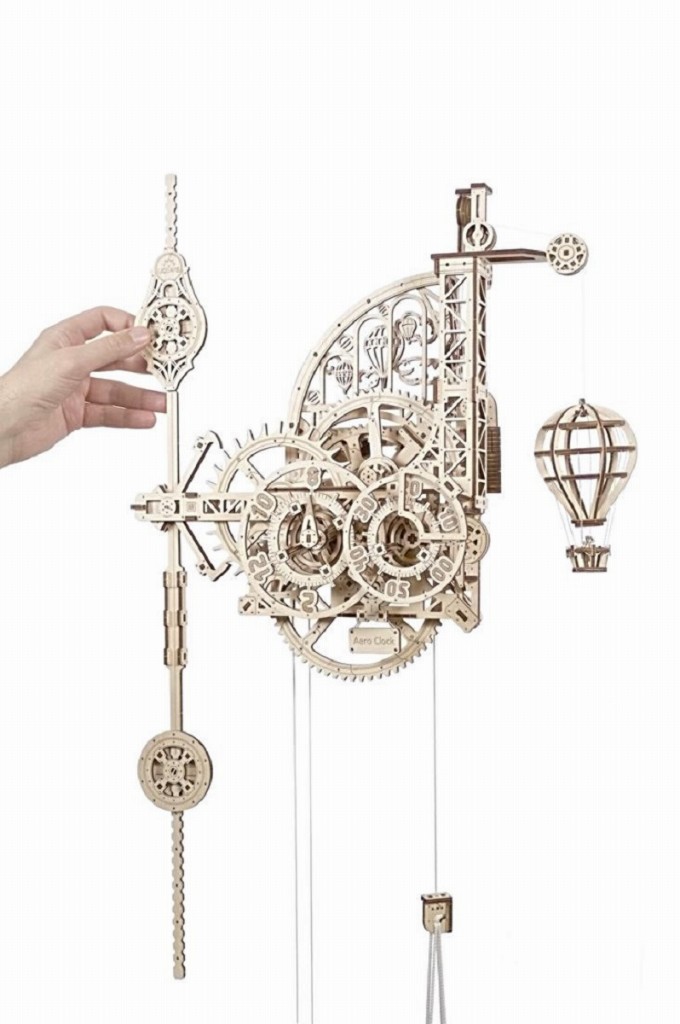
Ugears’ “Aero Clock”
Easy to make
The hurdles associated with designing and making parts may seem high, but for those keen to build their own karakuri devices, kits can make it easier. Jabez Japan, a wholesaler of imported goods, sells full-scale wooden assembly kits under its Ugears brand.
The “Old Clock Tower” mechanical model kit (¥1,870) has 44 components and is aimed at beginners. The clock can be assembled in about one hour and moves when the gears are turned by hand.
Meanwhile, the “Aero Clock” wall-mountable pendulum timepiece (¥11,880) has 320 components and typically takes about 11 hours to assemble.
“People can understand the mechanisms because they put them together themselves,” said Lee Jaesung of Jabez Japan. “Users can get a great sense of accomplishment because the finished product works and looks very cool.”
Kango Suzuki
Born in Miyagi Prefecture in 1993. Majored in product design at Tohoku University of Art & Design. His graduation project was titled “Kakidokei” (Time-writing clock), a clock that writes down the time. His social media videos have proved very popular. To find out more, visit his website (www.karakurist.jp).
"Culture" POPULAR ARTICLE
-
Maison Yoshiki Makes Paris Debut During City’s Fashion Week; Yoshiki Plays Piano as Models Walk Runway Near Eiffel Tower
-
KLP48 Debuts in Malaysia, Overseas Sister Group of Beloved Japanese Pop Idol Group AKB48
-
Indonesian Artist Eko Nugroho’s Embroidered Paintings Urge for ‘More Love Above The Peace’; Pieces Explore Politics, Social Issues of Indonesia
-
More Attention Sought for Creators of Atomic Bomb Paintings; ‘Hiroshima Panels’ Exhibited Around Japan and in 20 Countries
-
Kawamura Memorial DIC Museum of Art to Close from March; Options for Downsizing or Shutting Down Being Weighed
JN ACCESS RANKING