Steelmakers Face High Bar for Decarbonization
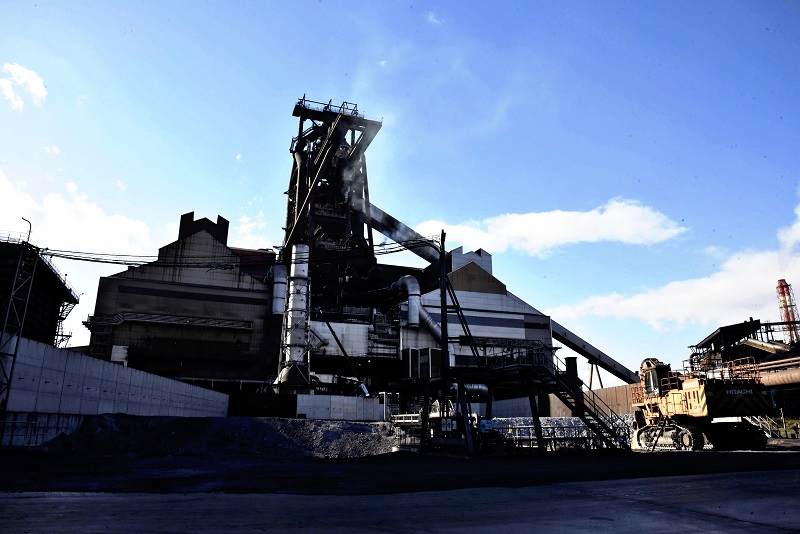
A blast furnace is seen in JFE Steel Corp.’s West Japan Works Kurashiki plant in Kurashiki, Okayama Prefecture, on Dec. 15, 2022.
10:50 JST, June 13, 2023
TOKYO (Jiji Press) — Major Japanese steel manufacturers are speeding up technology development and investment in a push to meet the challenging goal of decarbonization.
According to statistics compiled by the National Institute for Environmental Studies, carbon dioxide emissions from the steel industry account for roughly 50% of the total from the domestic industry sector. Decarbonization by steelmakers, therefore, is essential to Japan’s bid to achieve carbon neutrality by 2050.
The top three steelmakers operate blast furnaces, which produce steel by burning iron ore and coking coal. They are endeavoring to expand the size of electric furnaces, which emit less CO2 than blast furnaces do, and to develop a method for substituting hydrogen for coking coal in steel production.
JFE Steel Corp., a subsidiary of JFE Holdings Inc., has decided to shut down a blast furnace at its West Japan Works Kurashiki in Okayama Prefecture as early as 2027 and replace it with a large-scale electric furnace. CO2 emissions from electric furnaces, which melt and recycle scrap steel, are only about one-quarter of those from blast furnaces per production amount.
The company will close the No. 2 blast furnace, the oldest of the three units at the steelworks in the city of Kurashiki. It will continue to use the remaining two blast furnaces in order to maintain the production amount at the plant. President Yoshihisa Kitano said, “We will be able to reduce CO2 emissions by about 3 million tons annually.”
But steel output by electric furnaces uses a large amount of high-quality steel scrap as raw material. Kitano suggested that including scrap collection bases, the amount of investment needed for the shift is expected to reach at least several tens of billions of yen.
Industry leader Nippon Steel Corp. is also putting efforts into making use of large-scale electric furnaces.
In October last year, the company started commercial operations of a new electric furnace at its Setouchi Works Hirohata Area in Himeji, Hyogo Prefecture.
With an annual production capacity of 700,000 tons, the new furnace mainly produces electrical steel sheets for automobiles. It is the world’s first electric furnace capable of integrated production of high-quality electrical steel sheets.
Nippon Steel will also work on technological innovation for blast furnaces.
At the No. 2 blast furnace in the East Nippon Works Kimitsu Area in Chiba Prefecture, the company is preparing to conduct a demonstration test for cutting the volume of coking coal and instead using hydrogen gas for combustion.
"Business" POPULAR ARTICLE
-
Aviation Fuel Shortage Causes Problems at Regional Airports; Growing Demand, Lack of Workers to Transport
-
Prices of over 10,000 Food and Beverage Items to Rise This Year; Figure is down from over 30,000 Last Year
-
Sony Group to End Production of Blu-ray Discs; Market Has Shrunk Due To Growth Of Hard Disk Drives, Streaming
-
AI-Equipped Energy Efficient Air Conditioners Grow In Popularity; Some Can Guess Users’ Moods, Automatically Adjust Temperature
-
Toyota to Introduce 4-Day Workweek for Some Employees; Company Hopes More Flexible Schedules Will Boost Worker Motivation
JN ACCESS RANKING