Kawasaki Heavy’s president eager to develop epoch-defining technology
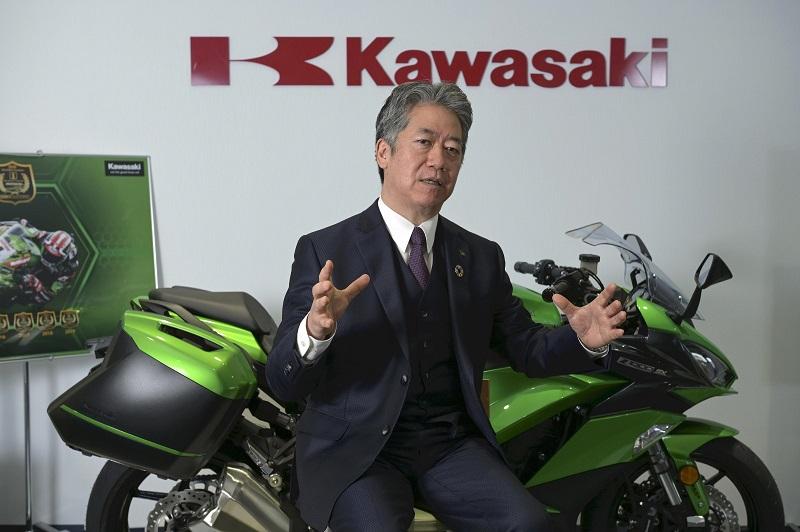
Yasuhiko Hashimoto speaks during an interview in Chuo Ward, Kobe, on Feb. 24.
18:21 JST, April 12, 2021
Kawasaki Heavy Industries, Ltd. wants to change society through the use of automation technologies and hydrogen energy. Leading the way is former robotics developer Yasuhiko Hashimoto, the president of KHI. He talked to The Yomiuri Shimbun about some of the company’s latest initiatives. The following is excerpted from the interview.
Hashimoto loved the hit manga comics “Astro Boy” and “Tetsujin 28” when he was a child. He used to draw structural plans of robots in the margin of his textbooks.
My father and brother were both doctors. When I was thinking about what to study, I wondered whether I should go to medical school. My father advised me to “pursue a career in a field that you like,” so I opted for the engineering department.
At university, I was engaged in volunteer activities, supporting patients with muscular dystrophy. At that time, the mother of an elementary school child suffering from the disease told me she wasn’t able to sleep for more than two hours straight because she needed to check on her child regularly. The experience made me want to someday create robotics that could be useful in the fields of medical and nursing care.
It was not until I started job-hunting that I learned about Kawasaki Heavy Industries, Ltd. The company has headquarters in Kobe, where I’m from. I learned that the company was the leading manufacturer of hydraulic robotics that were used at automobile plants, so I decided to join the company.
My first assignment at the company was to improve welding robots used to manufacture vehicle chassis. After analyzing the vibrations of the robot’s body and changing its design, the vibrations were eliminated completely. The company must have been satisfied with the results because I was transferred to the design division.
In 1995, Hashimoto proposed branching out into robotics for semiconductor manufacturing and spearheaded a new project.
It was at a time when the company was performing very poorly, and it was difficult to attract new customers. Although there was some opposition within the company, I presented the merits of my proposal, explaining that as we moved closer toward an IT-based society, the semiconductor business would grow significantly.
Because more than half of the semiconductors were supplied by U.S. firms back then. The only way to expand our business was to go to the United States.
When I presented my proposal to the head of the projects division, I was asked what kind of scale I was aiming for. I replied, ¥1 billion in annual sales, but I was told that the idea would be supported if we aimed at realizing annual sales of ¥10 billion. That sealed it for me.
I went to the United States in 1999, and in October 2000, we received specifications from a leading company to develop a product. The next three months were spent on development, followed by two more months on refinements. Our product was finally adopted by the company, but on the condition that we opened an office there, and attend the company’s meeting every week. I ended up being stationed in the United States for eight more years.
Once, a client said that one of our robots was not user-friendly because it would slip out of position if something knocked into it.
I argued that the problem was what or whoever was knocking into the robot but the person in charge said: “That’s a fair point, but there are people who want to replace the Kawasaki robots. You can say the right thing and be replaced by another manufacturer, or you can address the problem and we can keep using them. The choice is yours.”
It was a startling response that triggered a reaction. We worked hard to develop a robot that was more robust and resistant to impacts, along with the software for such products.
This taught me the importance of staying close to customers and responding to their needs.
After that, our reputation spread, and we achieved annual sales of ¥10 billion in 2006, four years earlier than originally targeted.
It was not because the team was made up of exceptionally talented individuals. We were able to exert a great deal of power because we were all determined to do whatever it took to satisfy our customers.
We also learned a lot about development methods. Instead of personnel spending a long time developing products, we had customers appraise projects that were 70-80% complete and then used their opinions to complete the product. This ultimately led to shorter development periods.
Hashimoto assumed the presidency of the company after the outbreak of the novel coronavirus pandemic. KHI is refining technologies that will contribute to the shift toward a telecommuting-based society.
Most employees who can telecommute are engaged in desk work. Telework is considered impossible for those on the front line of medical care services, and those engaged in the distribution of goods and construction. But I think the time will come when even these kinds of jobs can be done remotely. A promising solution to this problem is skill transfer learning systems that can transfer human skills to robots.
Artificial intelligence (AI) systems can be used to turn the abilities of technicians into data. We are in the process of introducing such technology at some of our production and processing sites.
Hinotori, Japan’s first domestically developed robotic surgery assistance system, was developed by Medicaroid Corp., a joint-venture firm founded by KHI and medical device maker Sysmex Corp. By accumulating digitized data of the surgical operations of skilled doctors, it will be possible to teach skills to new doctors.
In the development process, I observed several surgical operations. Our research on the movements of doctors resulted in the compact placement of the robot’s four arms. By enabling the free movement of an endoscope and forceps attached to the arms, the robot can perform precise operations that would be difficult for humans to do by hand.
We are also developing a robot that can automatically conduct PCR testing. The robot will be able to handle such tasks as sample collection, analysis and processing remotely, protecting medical workers from the risk of infection.
The shortage of manpower in the logistics industry due to the declining birthrate and aging population will be solved with advanced transportation devises using remote technology.
For example, an unmanned helicopter will fly to the delivery destination, and a robot will exit the craft to deliver a parcel to the recipient’s front door.
Urgently needed goods such as medical supplies could be delivered in a short time, even to remote islands and mountainous areas. By combining various technologies such as remotely operated robots, helicopters, off-road vehicles and motorcycles, the scope of solutions will expand.
KHI is also leading the way in the utilization of hydrogen, which is considered the “ultimate clean energy” as it emits no carbon dioxide when burned.
To use hydrogen cheaply to protect the global environment, it is essential to build a supply chain. Chilling hydrogen refined from low-quality coal mined in Australia to a temperature of minus 253 C, liquefies it and reduces the cubic volume by a factor of 800. The liquid hydrogen can then be transported to Japan by ship and used as a fuel for power generation or automobiles.
We are the only company in the world that has an entire chain of relevant technologies. In particular, we are expediting efforts to develop a large liquid hydrogen carrier, which will be key for the propagation of hydrogen-based energy.
To propel these new types of business projects, we plan to change our personnel system, promoting workers who are eager to tackle new challenges. Our slogan is “Changing forward.” [In Japanese, “kawaru” means “change” and “saki” means “forward,” which is a play on the pronunciation of the company’s name.] And we are calling on workers to change themselves first.
If you change the way you work and interact with people, you will be recognized for your value, but if you think that someone else will do it for you, there is no way you can move forward.
Rather than following the changes taking place in society, we should be swiftly creating and presenting new values. We have to be the ones who are creating the new era.
Whether it’s medical robots or the transportation and storage of liquefied hydrogen, the goals will be technologically very difficult to achieve. But if we succeed, we will be able to create tremendous value. It is our company’s mission to embrace challenges through such business projects.
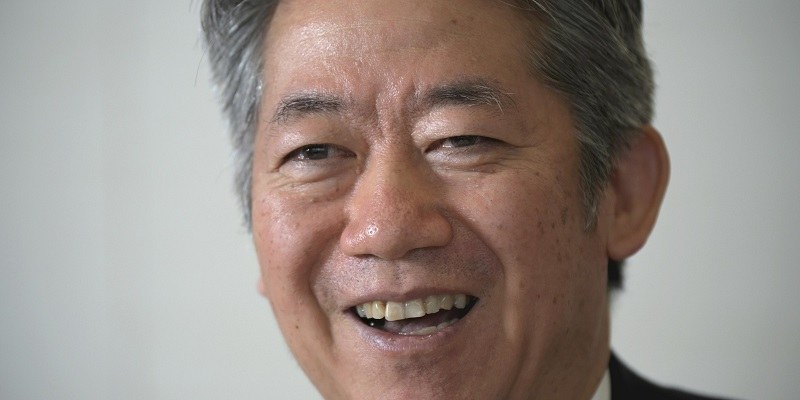
Yasuhiko Hashimoto
President of Kawasaki Heavy Industries, Ltd. Born in 1957 in Kobe, Hashimoto graduated from the University of Tokyo’s Faculty of Engineering and joined KHI in 1981. Having served as an executive officer, director and managing executive officer, he has been in the current post since June 2020.
"Business" POPULAR ARTICLE
-
Aviation Fuel Shortage Causes Problems at Regional Airports; Growing Demand, Lack of Workers to Transport
-
Prices of over 10,000 Food and Beverage Items to Rise This Year; Figure is down from over 30,000 Last Year
-
Sony Group to End Production of Blu-ray Discs; Market Has Shrunk Due To Growth Of Hard Disk Drives, Streaming
-
AI-Equipped Energy Efficient Air Conditioners Grow In Popularity; Some Can Guess Users’ Moods, Automatically Adjust Temperature
-
Toyota to Introduce 4-Day Workweek for Some Employees; Company Hopes More Flexible Schedules Will Boost Worker Motivation
JN ACCESS RANKING