Automation and AI take root in Japan’s veggie factories
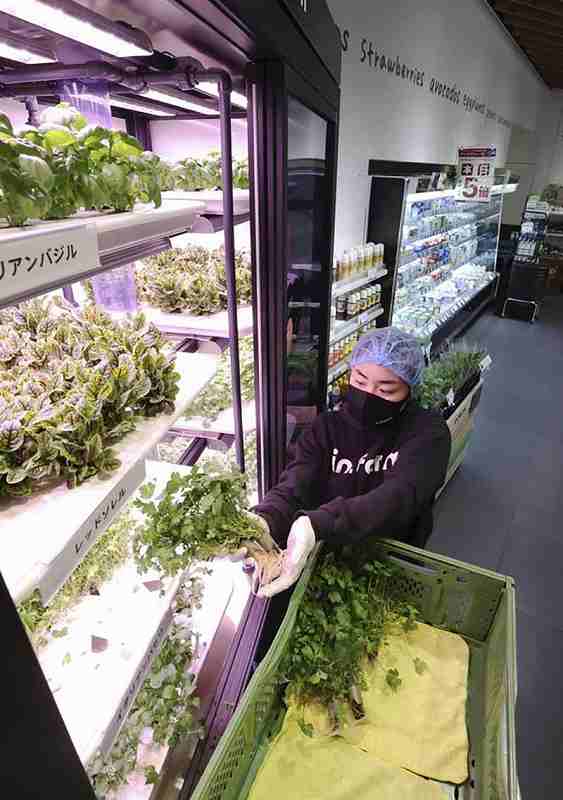
A supermarket worker harvests vegetables grown on-site in a glass case, in Minato Ward, Tokyo, on Oct. 26.
November 16, 2021
Vegetables grown in factories with the help of information technology to control temperature, light and other conditions have taken root in Japan.
As of February, about 390 vegetable factories were operating nationwide, about four times the 93 factories in 2011. Reasons behind the surge include significant technological advancements in automation, which are now able to handle veggies from their seedling to harvesting states.
As such factories are not directly affected by weather conditions and require fewer staff than their outdoor counterparts, their future use is expected to grow.
Big business enters the market
At the Kinokuniya International Supermarket Aoyama store near Omotesando Station in Minato Ward, Tokyo, parsley and herbs are grown inside the store under LEDs in a 2-meter-wide by 2-meter-high glass case.
The plants, grown hydroponically, do not require chemical pesticides. Seedlings are planted and vegetables are harvested twice a week, which are then sold on the spot. As the produce is not loaded up and transported by vehicle, customers can purchase super fresh vegetables with less harmful impact on the environment.
The commercial production of factory-grown vegetables kicked off in the 1980s and is primarily divided into two types: those that use artificial light, and those that use the power of the sun.
But recent developments include computers that precisely control humidity, carbon dioxide levels, nutrition and other factors.
“Vegetable factories are less affected by changes in weather,” said Hiroshi Fujimura, 62, secretary general of the Japan Greenhouse Horticulture Association. “And soil is not required if they use hydroponic culture.”
Aiming to diversify their business strategies, many large corporations have been entering the field.
Tokyo Metro Co. produces lettuce and other vegetables on land in Edogawa Ward, Tokyo, underneath a section of elevated Tozai Line railway tracks between Nishi-Kasai Station and Kasai Station. The company supplies the vegetables to hotels, restaurants and other facilities.
Chubu Electric Power Co. is now constructing a vegetable factory in Shizuoka Prefecture capable of delivering 10 tons of lettuce a day.
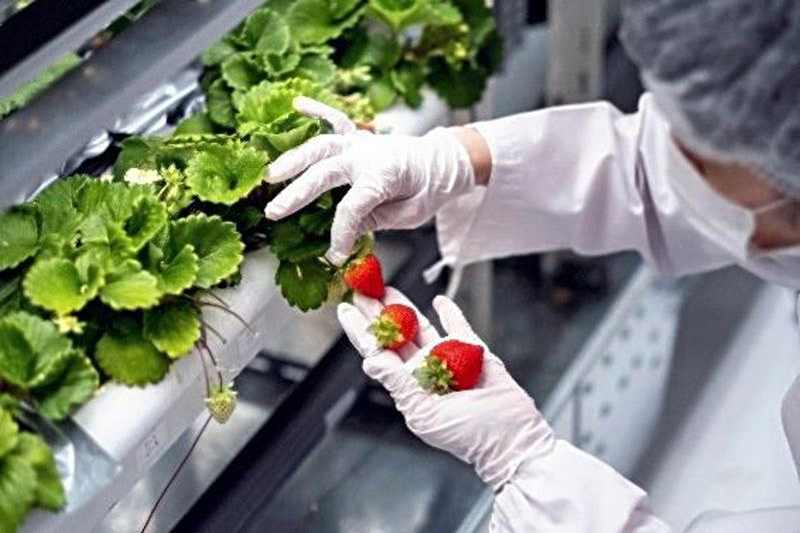
Strawberries are picked in a vegetable factory.
Remote-controlled factories
Vegetable factories can be remotely controlled.
German agricultural start-up Infarm is involved in 1,400 facilities in 11 countries including Japan. All facilities are equipped with sensors and the company measures and records the growth of all produce via cloud technology. Each factory’s lighting and other conditions can be individually calibrated based on analyses processed by the company’s artificial intelligence programs at their Berlin headquarters.
“Based on data, we want to pursue a farming method that requires less water, fertilizer and cost,” said Ikuo Hiraishi, 58, president of the Japanese arm of Infarm.
Earlier this year, the Niigata Prefecture-based Food & Agri Mechatro Solution Inc., which deals in industrial robots, built a lettuce-chopping device. The company has also developed a method that fully automates the processes involved in lettuce’s 40-day production cycle. A special container is used for the sprouts, which are then transferred to cultivation shelves and eventually harvested.
“The technology is expected to help significantly reduce labor costs,” said president Takuji Morita, 47.
Seasonless strawberries
Leafy greens comprise about 80% of all vegetables grown in factories utilizing artificial light. Such produce sees high demand year-round, does not require pollination and is easier to raise than fruit-bearing plants.
But in 2018, NTT Business Solutions constructed a strawberry factory in Osaka. Under the instruction of an agricultural cooperative from Sakawa, Kochi Prefecture, the company staff adjust temperatures, water plants and use bees for pollination.
“Strawberries are in demand throughout the year, as they are used for cakes and confections,” said Akiko Unami, 45, a section chief in charge of the business at NTT Business Solutions. “But the fruit is in short supply during the high-temperature period between June and November. While we’re aware that it is more difficult to grow strawberries than leafy greens, we see it as a challenge worth pursuing.”
Prices hit as high as ¥1,200 per strawberry weighing 35 grams or more.
At the Osaka factory, production is currently underway.
Eiji Goto, professor of environmental control engineering at Chiba University, said: “Vegetables produced in factories tend to be more expensive than those grown outdoors due to the initial investment of capital and utility costs. However, as they are very hygienic without any damage from pests, their use has spread to convenience stores and the restaurant industry. From now on, there will be fierce competition on the technological front to reduce costs and improve quality.”
"Science & Nature" POPULAR ARTICLE
-
Webb Directly Observes Exoplanetary CO2 for 1st Time
-
Japan Shipping Industry Increases Use of LNG Due to Difficulties Developing Next-Generation Fuel, Lower CO2 Emission Than Heavy Oil
-
4 Small Planets Confirmed Orbiting Nearby Barnard’s Star
-
Marimo Population in Hokkaido’s Lake Akan Dramatically Declined in Past 120 Years; 10-100 Times More Abundant Before
-
Physical Society of Japan to Hold ‘Quantum Fest’ in Tokyo in June; Event Marks 100th Anniversary of Quantum Mechanics
JN ACCESS RANKING