Heirs to Kyoto Talent / Handweaving Artisan Uses His Skill to Repair Cultural Properties
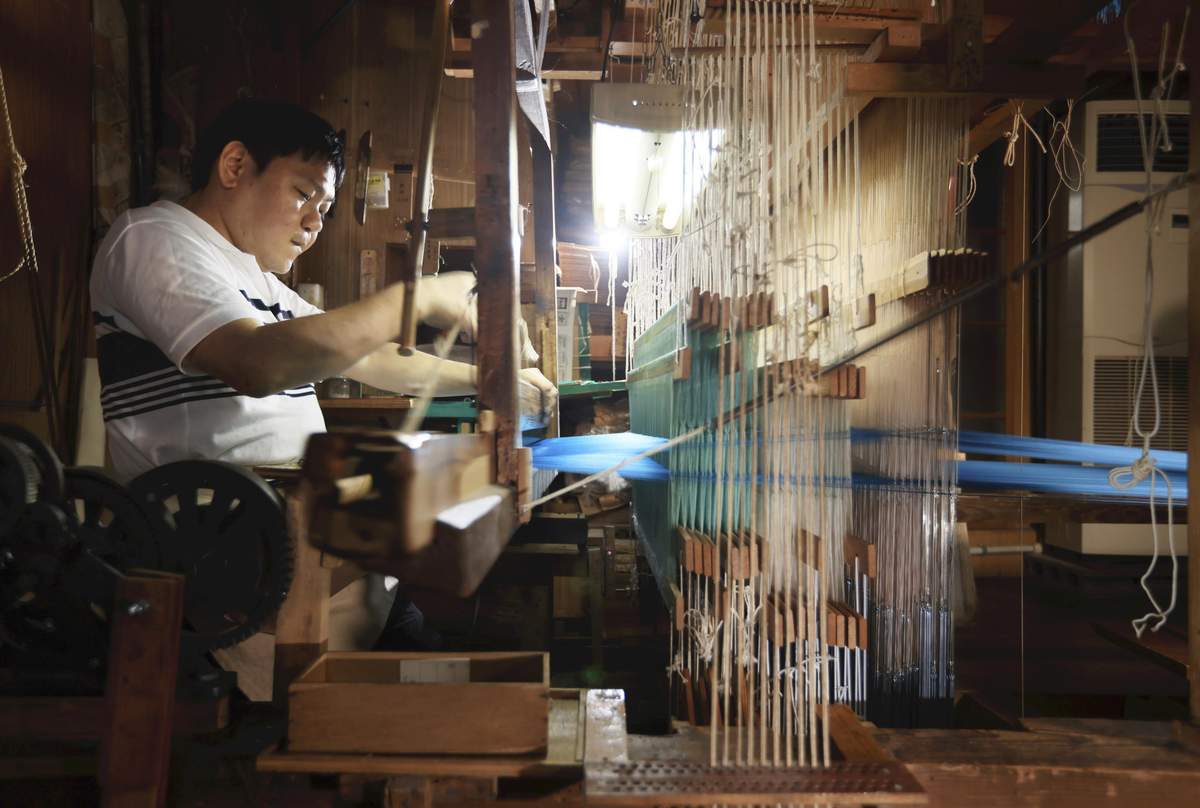
Junichi Hirose works on a loom in his workshop in Kamigyo Ward, Kyoto.
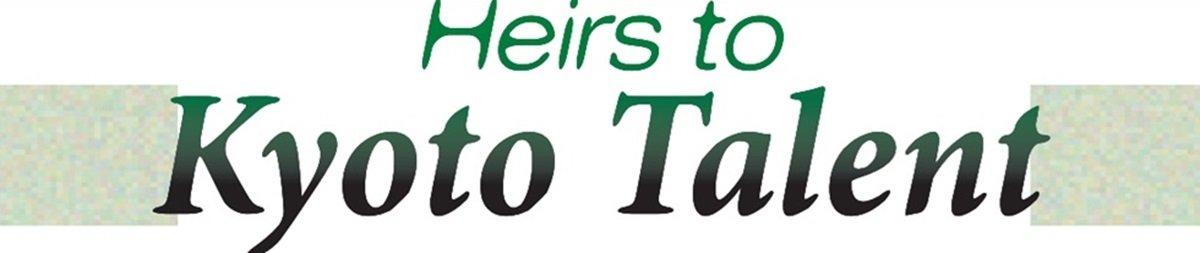
7:00 JST, December 9, 2024
KYOTO — An artisan briskly moves his hands and feet to the rhythmic clatter of a loom set with between 4,000 and 8,000 glossy warp threads in his workshop in Kamigyo Ward, Kyoto.
The workshop of Nishijin textile manufacturer Hironobu Orimono Co. is filled with colorful pieces of cloth called kire. Some are silk canvases for Japanese-style paintings and others are the decorative cloth used for making calligraphic works and paintings into hanging scrolls. The latter is called hyoso gire.
Kire are mainly used in the repair of cultural properties. For example, kinran cloth, decorated with patterns of plants and other motifs using gold thread, looks vivid and sophisticated, but has subtle designs so as to highlight paintings or calligraphy.
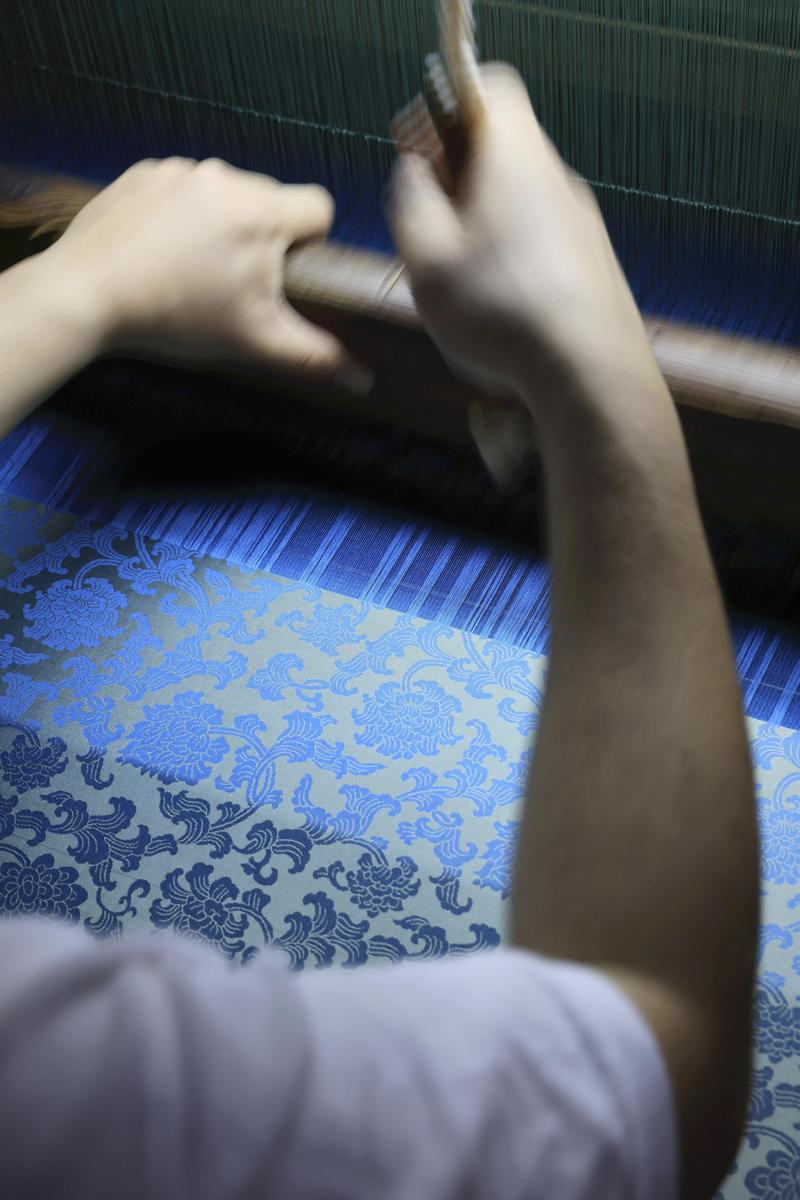
A beautiful pattern gradually appears under a pale light as Hirose weaves in his workshop.
Junichi Hirose, the fourth-generation owner of the long-established company founded over a century ago, is respected in his industry for his careful work and stable technique. He is also esteemed by people involved in the repair of cultural properties.
There are only five craftsmen in the nation, including Hirose, who can produce hyoso gire using the Nishijin handweaving technique.
Sudden takeover
Weaving involves a delicate and patient process. A weaver pulls up part of the warp threads by stepping on a pedal with their right foot before passing the weft thread through the warp threads, using a weaving shuttle. The weaver then beats the threads into place using a comb-like reed.
“The important thing in weaving is to maintain a rhythm and apply the right amount of strength,” Hirose said. He sharpens his senses to check the beating strength by the sound.
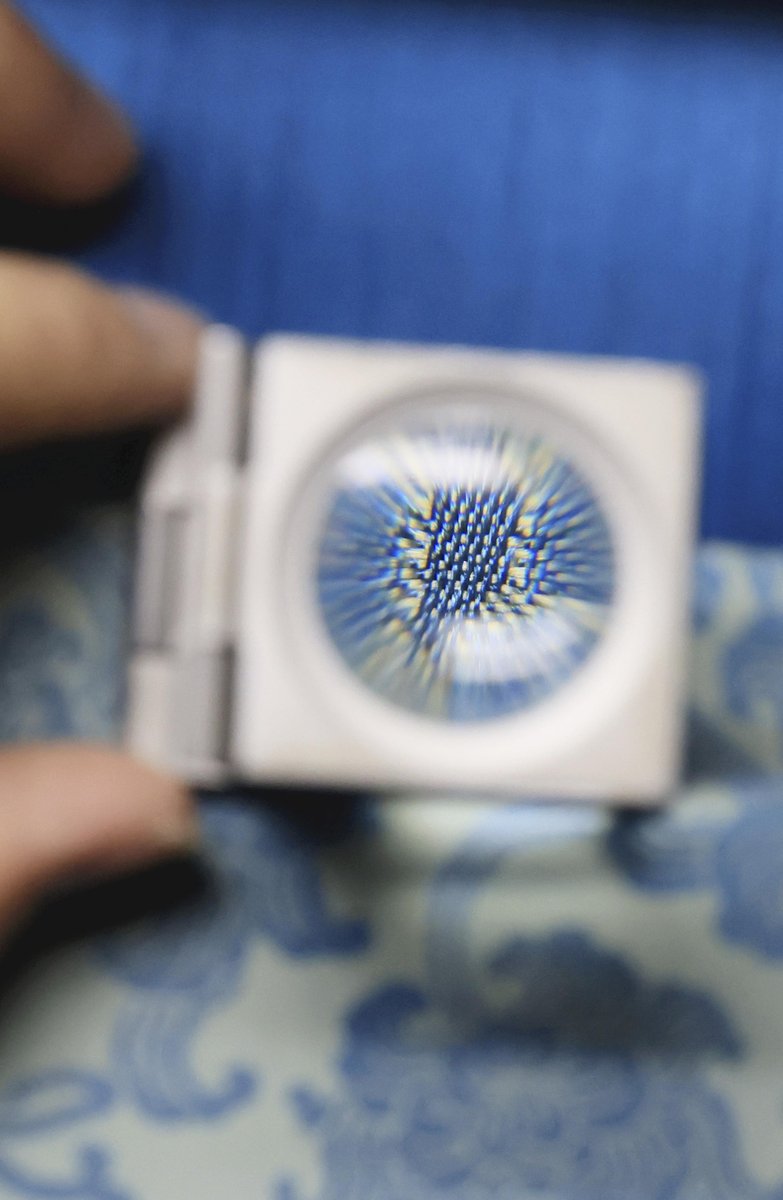
Details of a woven cloth are seen through a magnifying glass.
The manual work is essential to recreate ancient irregularities. According to Hirose, threads were uneven in thickness and color in the past, when everything was made by hand.
“Machine-made cloth is too uniform to strike a good balance with old calligraphic works or paintings,” he said.
Hirose took over the business at the age of 34 after his father died in 2017. His father Kenji was nationally certified as a Selected Conservation Techniques Holder in the reproduction of kodai gire, cloth used for ancient picture scrolls and other artifacts.
Hirose did not have enough time to prepare for the succession. He had been around the workshop since he was a child and had mastered the art of weaving as he had begun receiving serious training when he was 20 after graduating from a technical college.
However, there were many tasks of business owners that he was unfamiliar with, and the workshop fell in chaos.
The production work of hyoso gire scroll cloth is divided into various parts, such as dyeing, gold leaf production and raw silk thread procurement. As a general producer, textile manufacturers are involved in discussions with relevant parties to decide on such directions as the selection of materials and weaving styles.
Kenji had deepened his knowledge of the ancient cloth structure and the weaving methods through many years of research and restoration of the textile, so he was able to lead many projects to repair cultural properties. However, such wisdom had not been passed on to Hirose.
Hirose has been able to come this far thanks to the support of a cultural property preservation group that had a relationship with Kenji. The association aims to provide a stable supply of mounting cloth for the repair and restoration of cultural properties. It has been giving Hirose advice based on business operations done by his father and technical affairs, among other things.
Kenji recorded in notebooks his correspondence with clients and the progress of his cloth reproduction works. Hirose said they are extremely valuable assets for him, and he always uses them as a reference for his work.
Mounting a national treasure
In 2020, Hirose was chosen to be in charge of the production of cloth for mounting “Raigo of Amida (Amitabha) and Twenty-five Attendants,” a painting depicting Amida and 25 attendants as they descend from heaven on clouds over steep mountains. The 14th-century painting, held by Chion-in Temple in Kyoto, is designated as a national treasure.
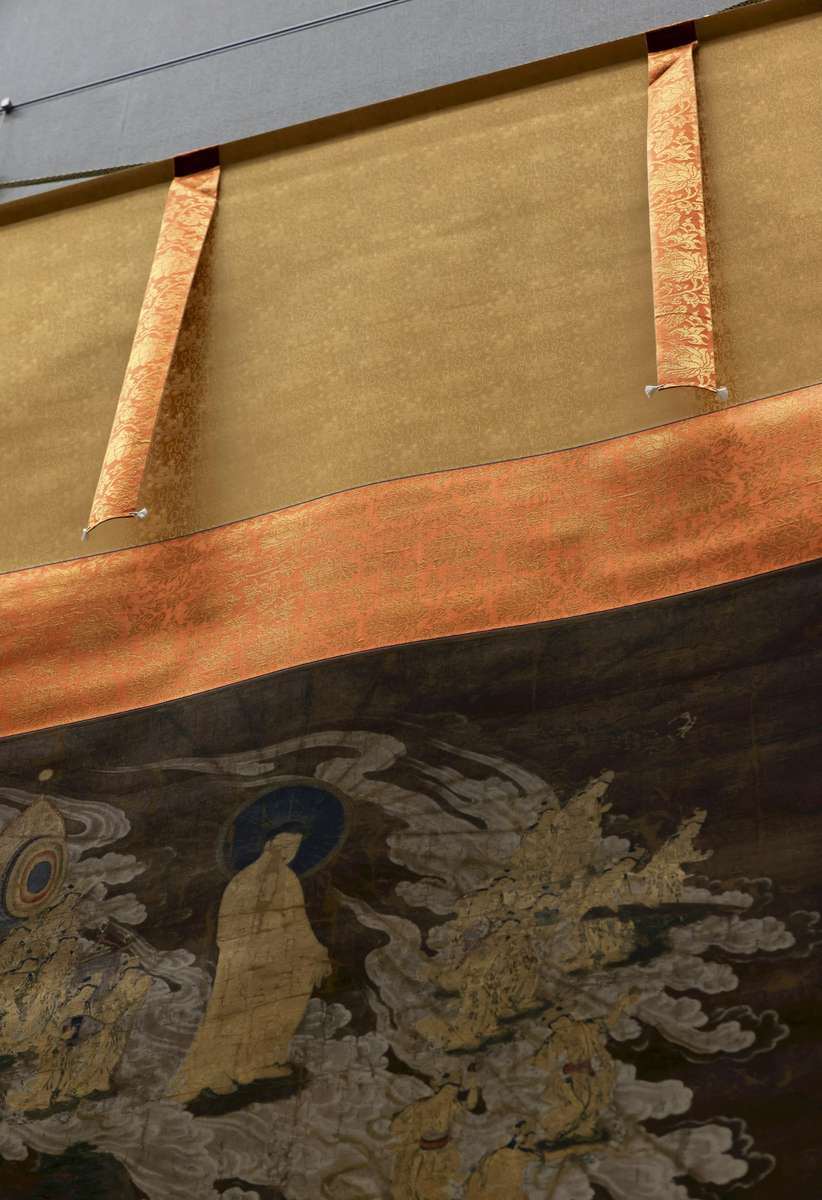
Part of the cloth Hirose made for the mounting of the painting “Raigo of Amida (Amitabha) and Twenty-five Attendants”
In order to create a cloth that matched the texture of the painting, Hirose tried a special weaving method that tends to make fabrics wavy. He went through a lot of trial and error because it was difficult to control the shrinkage of the fabric. After about a year, Hirose completed the cloth, which has a reddish hue and is decorated with lotus flowers and an arabesque design.
“About 90% of our work is usually completed by the time the threads and the design of the pattern for the fabric arrive at my place. All I needed to do is make the fabric with them,” Hirose said. “But that time, I could say I produced a wonderful cloth.”
Hirose is determined to carry on the tradition.
“I feel a sense of responsibility when I think that cloth I’ve worked on will be passed down as a cultural asset for a long time. I’ll absorb our ancestors’ wisdom and continue studying them.”
***
If you are interested in the original Japanese version of this story, click here.
"Features" POPULAR ARTICLE
-
Tokyo’s Female Rickshaw Pullers Draw Attention in Asakusa; They Attract Tourists Through Social Media Posts
-
CARTOON OF THE DAY (December 27)
-
200 Sheep Form Kanji for 2025 Chinese Zodiac Sign at Japan Farm; New Year Event to Take Place Weekends, Holidays through Jan. 26
-
CARTOON OF THE DAY (December 21)
-
CARTOON OF THE DAY (December 28)
JN ACCESS RANKING