Traditional Kyo-yuzen Dyeing Gives Flair to Modern Aloha Shirts
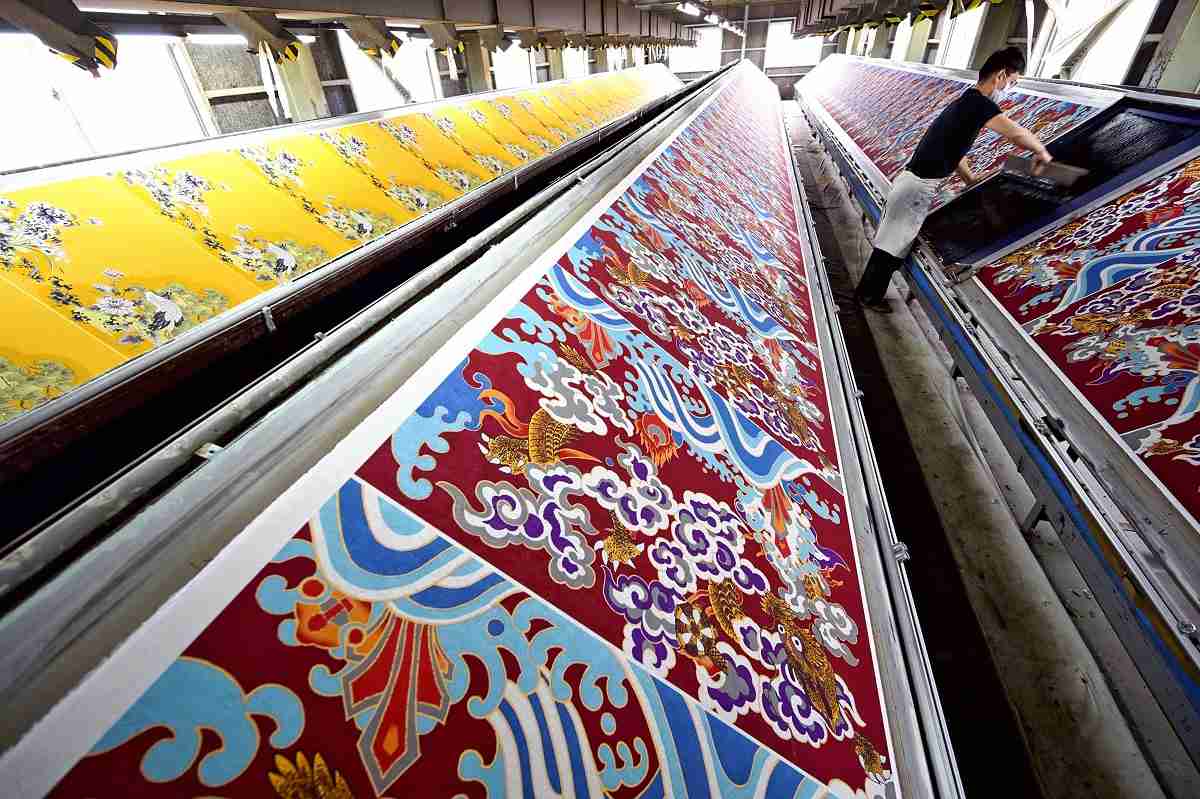
A craftsman at Kamedatomi Co. in Ukyo Ward, Kyoto, moves a framed stencil along a long piece of fabric.
12:37 JST, February 23, 2023
KYOTO — The dyeing technique is centuries old, but the products are anything but traditional. And they are flying off the shelves.
Kyoto-based Kamedatomi Co. has returned to its roots and adapted Kyo-yuzen to make Aloha shirts and T-shirts featuring a variety of colorful motifs and patterns depicting cranes, dragons and other auspicious symbols.
The firm’s lavish cut-and-sew items are inspired by kabuki costumes. Other goods feature designs inspired by the work of the great ukiyo-e artist Katsushika Hokusai and others under the company’s Pagong brand.
The firm, which was founded in the Taisho era (1912-1926) provides clothing with a modern feel based on traditional Japanese stencils used during its long history and which had been preserved in its warehouse.
The clothing has proved particularly popular among overseas tourists and young Japanese.
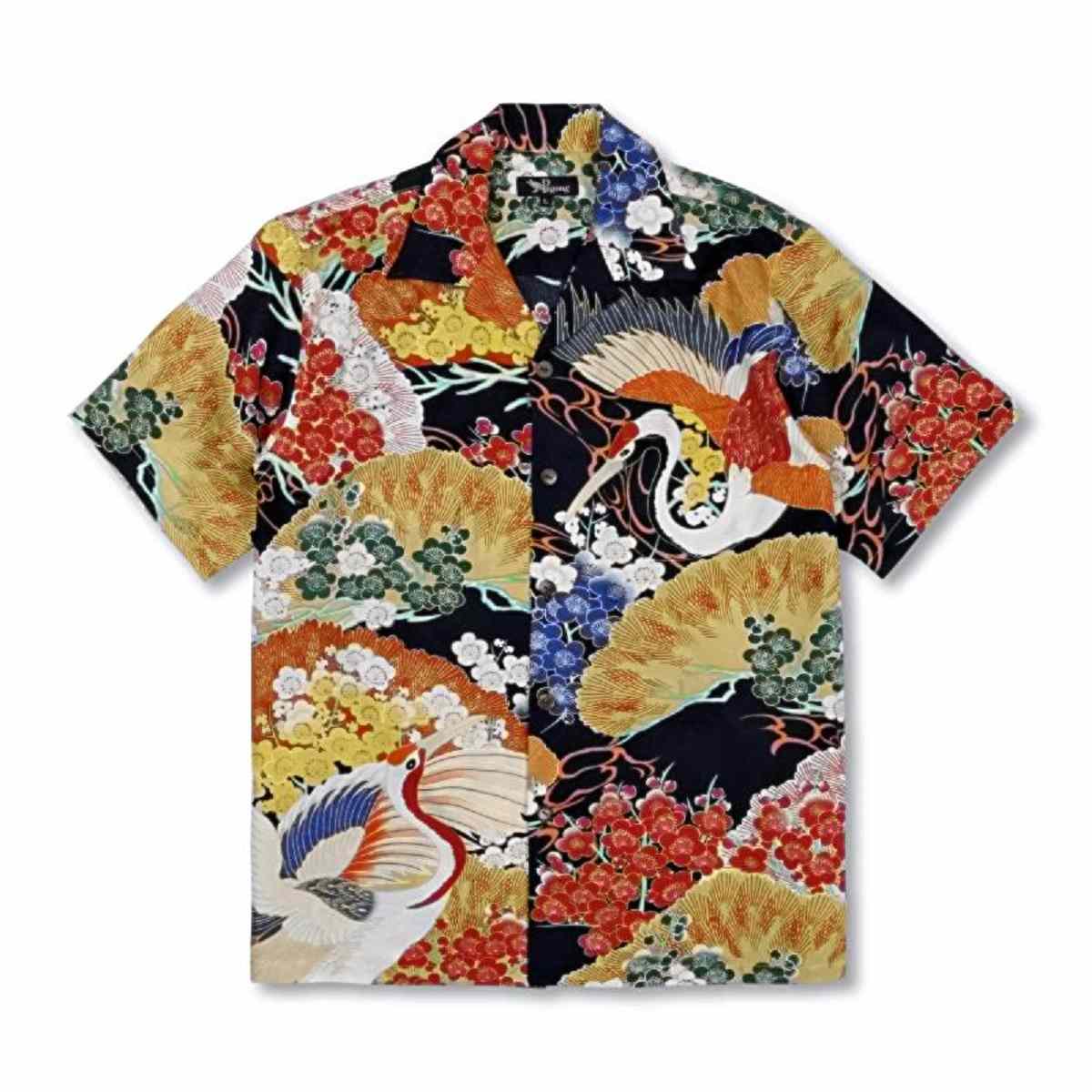
An Aloha shirt made using the Kyo-yuzen dyeing technique
Painstaking process
Recently, I visited the company factory where the fabrics are dyed.
Yuzen dyeing was invented in the Edo period (1603-1867). The factory uses a method called “kata yuzen,” in which each color is dyed by hand using a stencil.
Katsuhisa Yamada, 68, and Masayoshi Ono, 36, placed a wooden-framed stencil onto a section of tightly stretched white cloth measuring about 1.1 meters wide and 24 meters long, then spread dye on the cloth with a large rubber-bladed squeegee. The stencil was then moved along the cloth and the process was dexterously repeated.
During my visit, a dragon pattern was being created on silk cloth. Each time Yamada moved his hand, the outline of the dragon became clearer. A pair of eyes came into view and further shading was added, making the creature look almost three-dimensional. Each color has a different stencil, and for the dragon pattern, 10 stencils are used. Some complex, colorful patterns require as many as 25.
The factory utilizes more than 500 colors. Based on formulations handed down through the years, powder dyes are dissolved in hot water and blended with glues of different viscosity.
Great skill is required to achieve beautiful, blur-free finishes with each part of the pattern in place. The factory uses various fabrics, including silk, cotton and polyester.
“Each time I work on a new type of fabric, it’s a process of trial and error,” said Yamada, a craftsman with 45 years of experience.
Squeegees vary too — some have soft tips, while others have hard ones — and it is important to determine the correct one to use based on the material and the details of the pattern. Particular care is needed when dyeing satin or taffeta, as they are prone to uneven coloring.
Experience is key to this job. “Too much dye being absorbed is bad, while too little causes unclear patterns,” Yamada said. “It’s important to apply the right amount of pressure.”
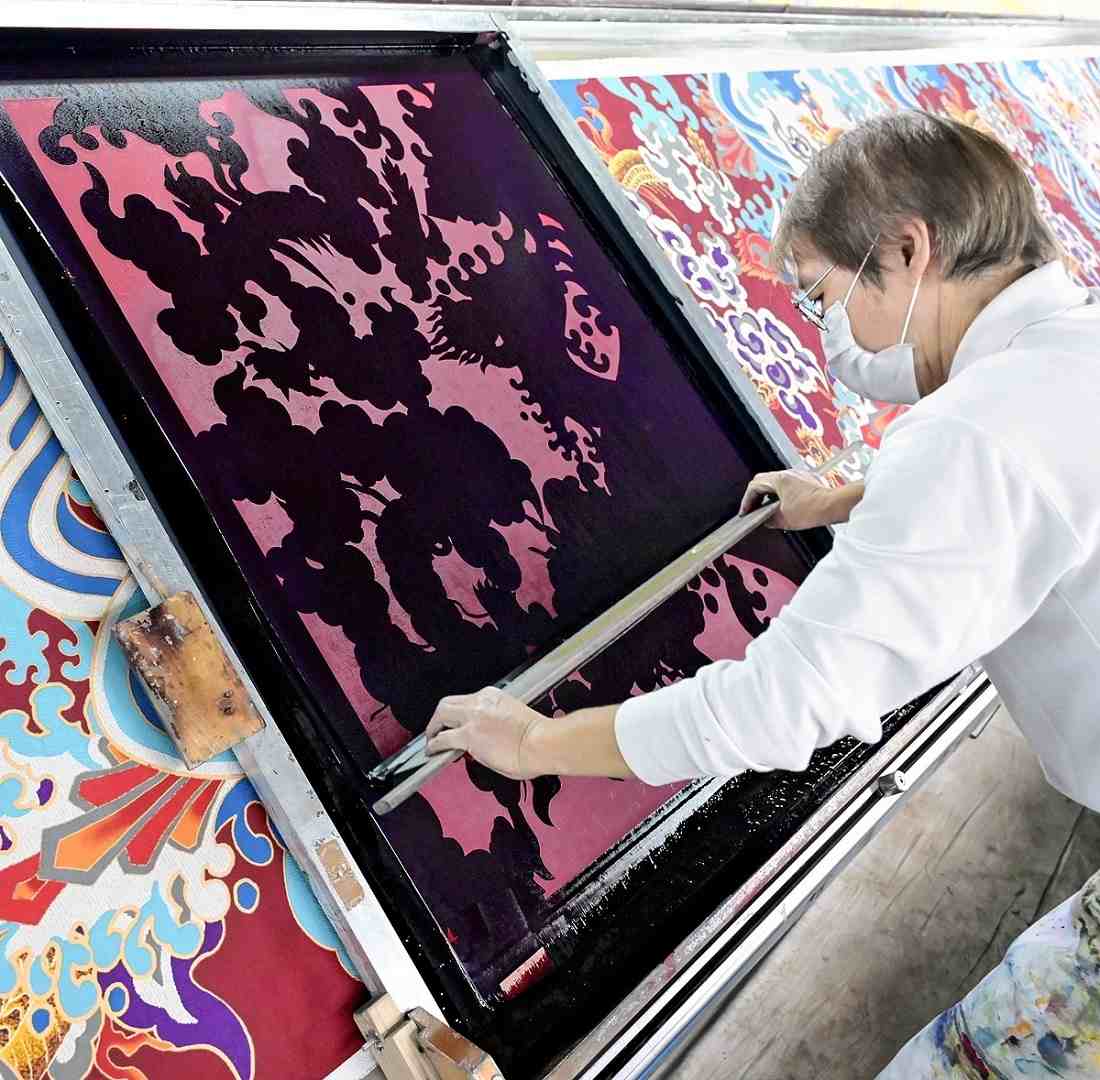
Katsuhisa Yamada uses a squeegee during the dyeing process.
Restoring tradition
Kamedatomi Co., which was established in 1919, employed more than 100 craftspeople in the early to middle part of the Showa era (1926-1989), when there was strong demand for kimono. In the following Heisei era (1989-2019), however, Japanese lifestyles changed and the company primarily dyed fabrics for Western-style clothing. It worked as a subcontractor and gradually decreased in size.
A turning point came in 2001, when Noriaki Kameda, 66, the fourth-generation head of the company, decided to once again use the 5,000 to 6,000 Kyo-yuzen patterns preserved in the company’s warehouse. The firm’s Kyo-yuzen Aloha shirts were well received when they first appeared on the market.
In recent years, inkjet printers have been increasingly used in the mass production of kimono and other clothing.
Tomihiro Kameda, 37, the fifth-generation head and current president of the company, said: “The charm of the kata-yuzen [technique] lies in the detailed patterns and beautiful colors. The deep colors and warmth can only be achieved by human hands.”
Kameda says the company will continue using the traditional techniques and pass them on to future generations.
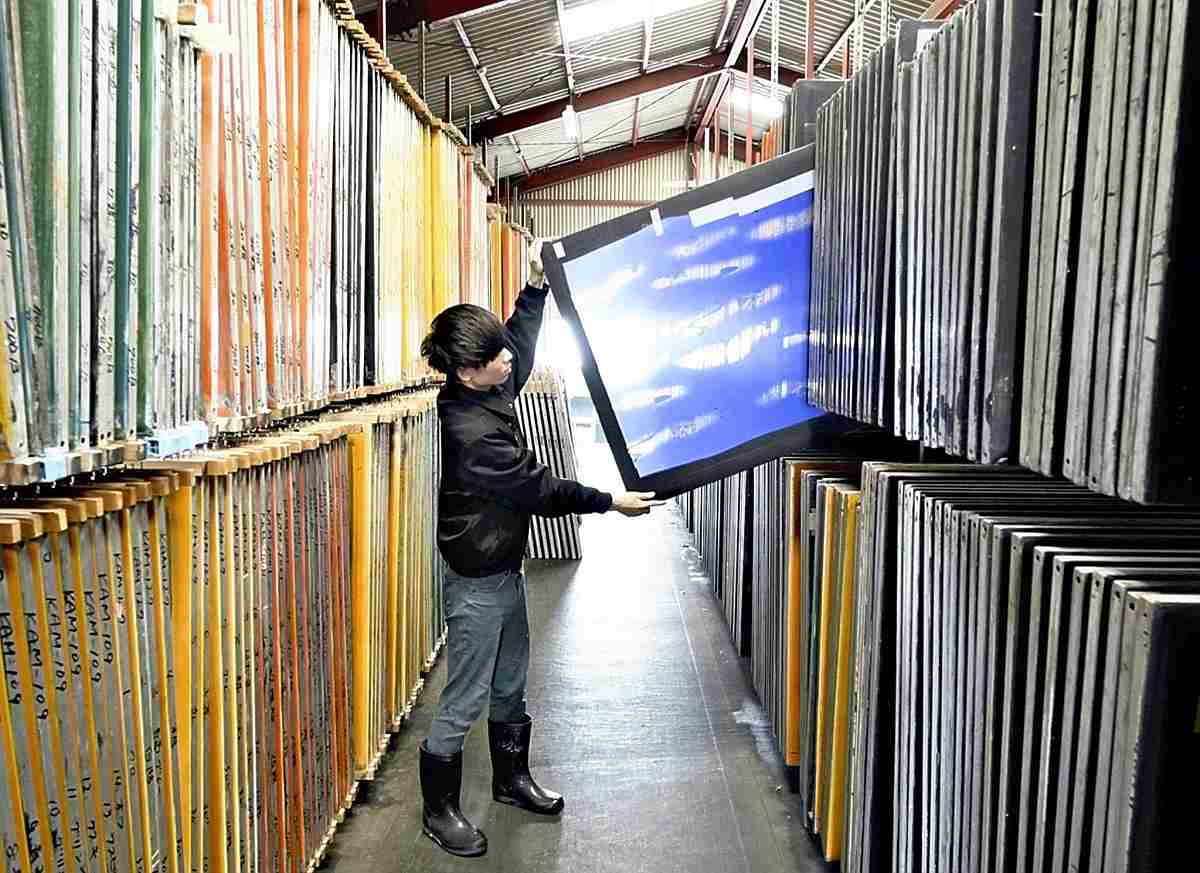
The company has more than 1,000 stencils for dyeing.
"Culture" POPULAR ARTICLE
-
Night Parade of Dinosaurs in Tokyo; Lifelike Dinosaurs to Stomp Their Way Through Tokyo National Museum
-
Ueshima Museum, A New Center For Contemporary Art, Opens In Tokyo; Displays Works By Present-Day Artists From Japan And Overseas
-
Art Museums in Japan’s Kansai Region Reopen After Renovations; Many Structures Need Work to Keep Up with Modern Times
-
Indispensable Craftsmanship for Producing Traditional Nara Sumi Inksticks; Going from Doughy Soot to Beautiful Ink
-
Bunraku Plays with Animated Backgrounds to Go on U.S. Tour; Featuring 9 Shows in 5 Cities
JN ACCESS RANKING