Toyota to Launch EVs with All-Solid-State Batteries by 2028
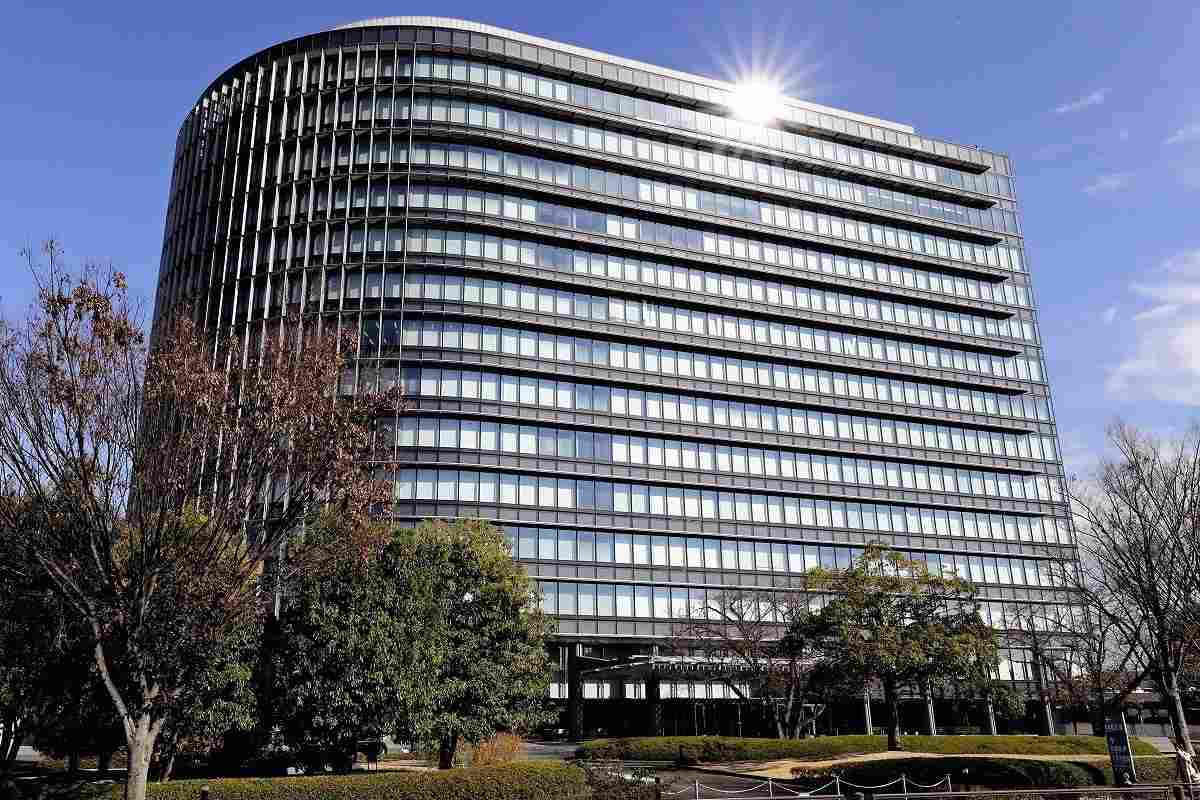
Toyota Motor Corp. headquarters in Toyota, Aichi Prefecture
16:34 JST, June 13, 2023
Toyota Motor Corp. has announced plans to launch in 2027-28 electric vehicles with all-solid-state batteries, next-generation technology that is expected to increase EV range and shorten charging times.
With automakers such as Tesla Inc. leading the EV market, Toyota hopes the new batteries will help it improve its performance in the sector.
All-solid-state batteries contain solid electrolytes, in contrast to the liquid electrolytes in the lithium-ion batteries currently used in EVs and electrical devices.
Benefits of the new batteries include high-power output, long range, short charging times and opportunities for miniaturization. However, issues to be addressed, include short lifespans and the need to mass produce the batteries at low cost.
The batteries will be installed in models being developed by Toyota’s BEV Factory, a new EV-focused unit.
Toyota aims to develop vehicles that can be charged from zero to full in less than 10 minutes with a range of 1,000 kilometers, about double the distance of conventional EVs powered by lithium-ion batteries.
Other Japanese automakers are also developing all-solid-state batteries, with Honda Motor Co. and Nissan Motor Corp. aiming to roll out models with next-generation batteries by the end of the decade.
To improve the competitiveness of EVs, “competitiveness of batteries is the most important [factor],” Honda President Toshihiro Mibe has said.
Honda will invest ¥43 billion to construct a demonstration line at its research facility in Tochigi Prefecture in spring 2024.
Meanwhile, Nissan is investing ¥140 billion to establish a prototype production line at its plant in Kanagawa Prefecture by fiscal 2024.
Toyota aims to sell 3.5 million EVs globally in 2030 — about 140 times the 2022 level — with 1.7 million vehicles expected to be next-generation EVs produced by BEV Factory.
The unit will implement a process called “giga casting,” using a single die cast for a part of the chassis that is currently assembled in 33 steps with 86 components.
Tesla has also adopted the method, which is expected to significantly reduce costs.
Toyota aims to reduce the number of manufacturing steps by half, by also introducing technology that will enable unfinished vehicles to move on its own from one stage to the next.
“Significant component integration can help reduce vehicle development costs and plant investment. This is the future of manufacturing.” BEV Factory President Takero Kato said.
"Business" POPULAR ARTICLE
-
Tariffs to Cause ‘Short-term Bumps,’ Trump Economic Adviser Tells Fox Business
-
Bank of Japan Gov. Ueda Says ‘Uncertainty Is Quite Large’
-
Mixed Feelings as Stockpiled Rice Arrives at Stores; In Spite of Expected Short-Term Price Relief, Worries Arise about Persistent Market Problems
-
Trump’s Auto Tariffs to Cover Hundreds of Billions of Dollars Worth of Vehicle, Parts Imports
-
Japan Big Maker Sentiment Worsens: BOJ Tankan
JN ACCESS RANKING