Wagasa-Making Classes Pass on Traditional Japanese Artisans’ Techniques, Philosophy to a New Generation
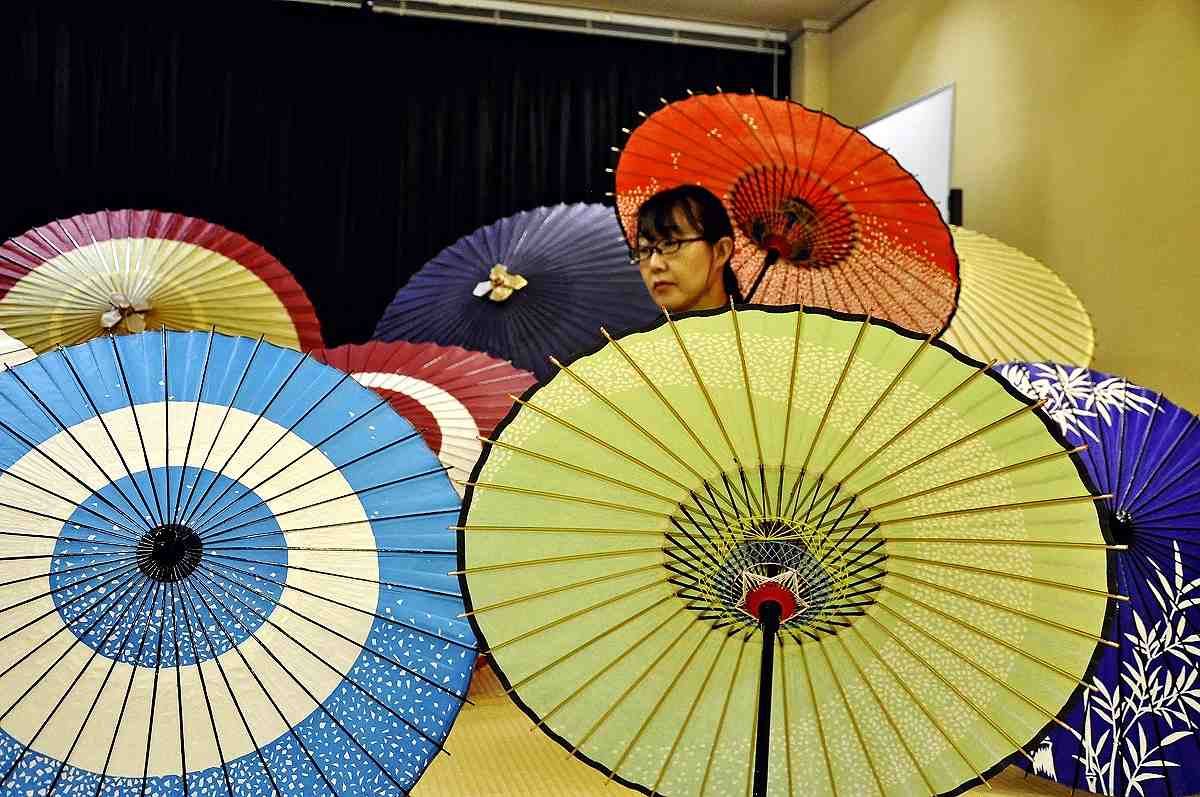
An artisan examines Mima wagasa traditional Japanese umbrellas in Mima, Tokushima Prefecture.
13:30 JST, October 27, 2024
MIMA, Tokushima — In the Wakimachi district of Mima, Tokushima Prefecture, stands a former castle town called Udatsu no Machinami (Udatsu townscape), which is designated by the government as an Important Preservation District for Groups of Traditional Buildings.
The town is home to Mirai Kobo, a workshop where visitors can experience making traditional Japanese crafts. This is also the place where craftsmen assemble Mima wagasa (traditional Japanese umbrellas of Mima). Production of Mima wagasa is said to have begun in the latter years of the Edo period (1603-1867).
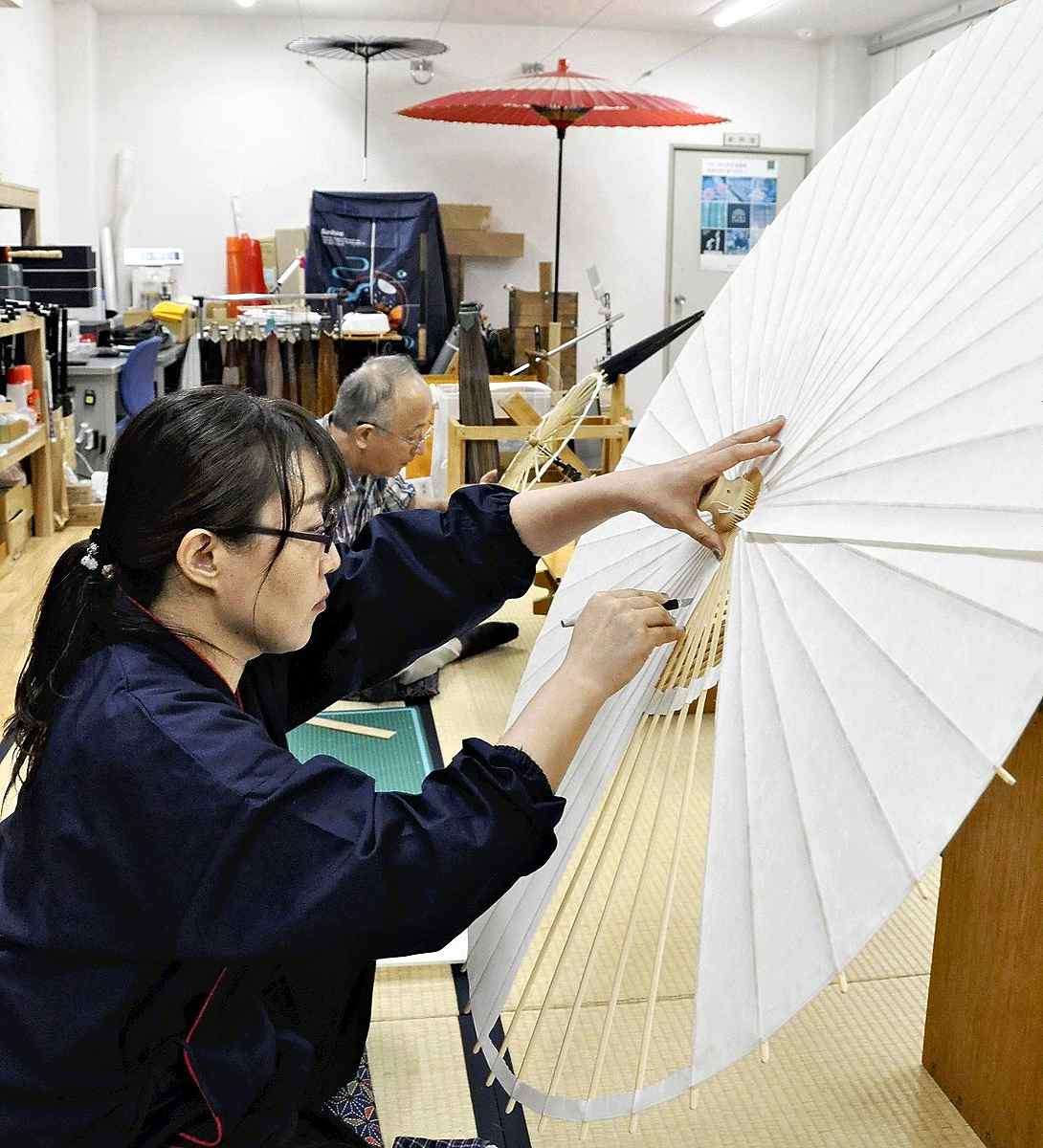
Artisans attach washi traditional Japanese paper to the ribs of Mima wagasa.
First, pieces of bamboo are cut and split to make ribs for the umbrellas. Threads are then used to connect the ribs, the stretchers supporting them and the top notch — the central part of an umbrella that helps it open or close. Washi traditional Japanese paper is attached to the ribs, each part is reinforced and fold lines are added on the canopy. After oil is brushed on the paper and the umbrella is dried in the sun, lacquer is brushed on the surface. All of this work is done by hand, so it takes about six months to complete a single umbrella.
One type of Mima wagasa is the janomegasa — a traditional umbrella with a spiral pattern and a slim shape, which is adorned with threads in five colors around the center on the inner side.
“What’s special [about Mima wagasa] is that they’re decorated in a rather flashy way,” said Satoshi Sumitomo, 65, quietly. He is the head of a group of Mima wagasa makers.
The city’s Koozato district used to be a production area for Mima wagasa. Immediately after the end of World War II, there were more than 300 umbrella manufacturers there, producing nearly a million Mima wagasa every year. But they lost ground to Western umbrellas and followed a course of decline. Today only a few dozen wagasa makers continue to operate in the whole country.
It was in 2011 that the city’s chamber of commerce and others started holding a course to train “meisters” (masters) of Mima wagasa making.
Fifteen people participated in the course, which was taught by an elderly woman who had been making Mima wagasa by herself. Some of the participants decided to form their own group of Mima wagasa makers in the following years.
“Even though we were taught well [how to make Mima wagasa], the tradition will be lost if we don’t work on it, I thought,” recalled Kanako Morishita, 50, who served as the group’s first leader.
They learned how to make wagasa parts by watching old films and studying old source materials. When they needed machinery, they restored available products by themselves. Wagasa making requires precision. The holes for threading must be precisely measured in units of 0.1 millimeters, and the task of shaving ribs to the right thickness is very delicate. After a process of trial and error, they started selling Mima wagasa umbrellas. Clients include traditional Japanese restaurants, acrobats spinning umbrellas and the Mima municipal government, which uses the umbrellas as gifts in return for “furusato nozei” hometown tax donations and presents for children celebrating their first birthday in the city.
A large janomegasa, with 48 ribs, is priced at ¥50,000.
“There are only a handful of orders from individual customers.” Sumitomo said frankly, adding, “But…”
Unlike Western umbrellas, which open with just one touch, a wagasa umbrella requires a user to turn the shaft and put a hand inside to open it. What an elegant gesture, and how carefully prepared the finished products are!
But wagasa makers that have lasted for generations are disappearing from the city, which prompted Sumitomo’s desire to prevent these pieces of traditional Japanese culture from becoming extinct.
The group has held wagasa making classes at local schools, wagasa experience events for tourists and artisan training courses to nurture successors to take over the wagasa tradition, through which new members started coming to Mirai Kobo. The workshop is planning to go to other prefectures in Shikoku region to teach and spread traditional techniques and philosophy.
"Society" POPULAR ARTICLE
-
Record 320 School Staff Punished for Sex Offenses in Japan
-
Miho Nakayama, Japanese Actress and Singer, Found Dead at Her Tokyo Residence; She was 54 (UPDATE 1)
-
Central Tokyo Observes 1st Snow of Season; 25 Days Earlier than Last Winter
-
Risk of Nuclear Weapons Being Used Greater Than Ever; Support Growing in Russia As Ukraine War Continues
-
Overtourism Grows as Snow Cap Appears on Mt. Fuji; Local Municipalities Hard Pressed to Establish Countermeasures
JN ACCESS RANKING