Hearts and feet go into crafting Nara ink sticks
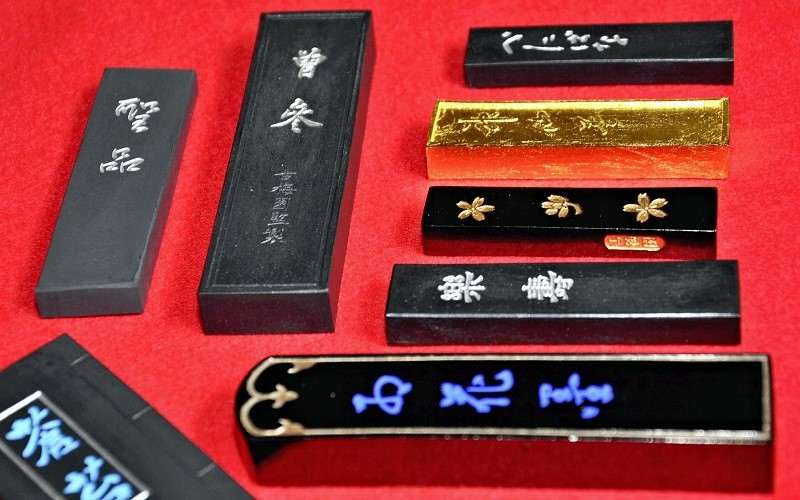
Various types of ink sticks produced by Kobaien, including Kokaboku, front right
18:00 JST, June 5, 2021
NARA — Sometimes an ink is not what you think. For the sumi ink used in Japanese calligraphy, this is most likely the case. This particular type of ink is not liquid, but starts as a solid stick, created through extraordinary craftsmanship, that is ground against the surface of an inkstone with water.
More than 90% of Japan-made ink sticks are produced in Nara, and the products have been established as a brand known as Nara Sumi.
I visited Kobaien, a long-established ink maker, where five craftspeople were working hard at their humble task of producing ink sticks using the traditional method.
The ink-making method, which was introduced to Japan in 610, is believed to have been brought by a monk from the Korean Peninsula. It then developed in Nara. Kobaien was established in 1577, even before the Edo period (1603-1867) began.
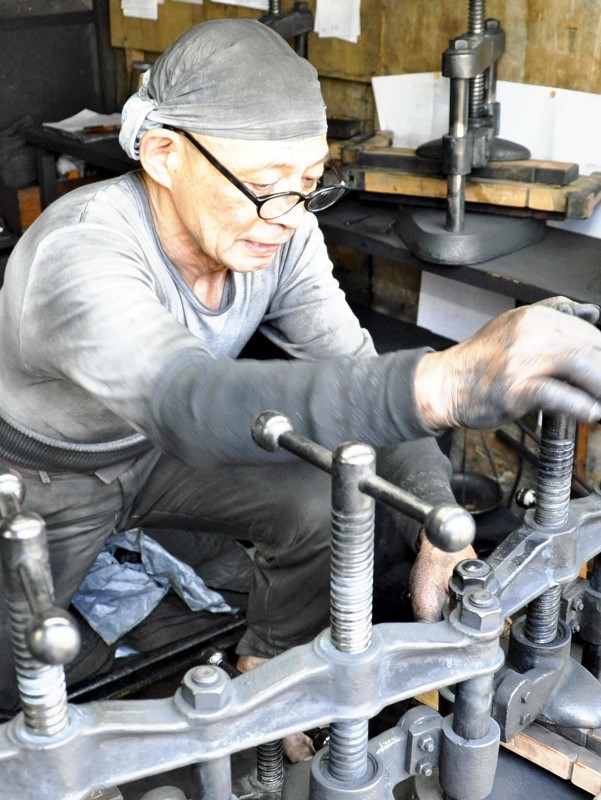
A Kobaien craftsman presses soot dough into a mold after the kneading process in Nara.
At the Kobaien factory, I saw the craftspeople vigorously kneading a small mass of black dough with their hands, before stepping on it with their bare feet and tearing it to knead it again. They were stepping on it so hard that I could hear the sound from their actions. Their hands, feet and even their clothes were all blackened. It was as if they were wrestling with the dough.
Nara Sumi is produced by kneading a mixture of gelatin and soot, and letting it dry for months.
The soot is collected by burning oil. Kobaien has a windowless storehouse with four rooms inside for collecting the soot. In each room, there are 100 containers each filled with rapeseed oil and a wick made of woven rush.
Soot accumulates inside the lid placed over each flame. The amount of soot collected a day is enough raw material to make 50 to 100 ink sticks.
This method of making ink sticks by using oil smoke is said to date back to around 1400, when it was first done at Kofukuji temple in present-day Nara. The soot collected using this method is left to sit for five to 10 years before being mixed with a gelatin solution.
“It is important to knead the soot dough well, so that it does not bend when it gets dried and its surface becomes smooth,” said Daiji Motohashi, 56, the factory manager.
The well-kneaded dough is pressed inside a wooden mold and buried in ashes to let it dry. First, damp ashes with a lot of moisture are used, then replaced with ashes with less moisture. Drying takes a week for a small stick, and 30 to 40 days for a large one.
Tied with straw, the ink sticks are hung from the ceiling and left to dry naturally for another one to six months. After this, the ashes are washed away with water, then the surface is polished to make it look smooth and shiny. Finally, gold or silver powder and pigments are applied to complete the whole process.
“Every step in the process is important,” said Motohashi. “Passing the baton from one task to another with absolute certainty will naturally result in a fine product.”
Value increases with age
An ink stick can take form in as little as six months, but it could take four to five years to make it a marketable product. Ink sticks are believed to become better with age, making older ones much-prized. Some pieces are said to be about 100 years old.
“Unlike ordinary products, we can’t produce ink sticks readily just because the stocks run out. Having said that, it’s no good if we have too many in stock,” said Susumu Takesumi, 61, the sales manager of Kobaien. “We have to manufacture our products from a medium- to long-term perspective.”
Kokaboku, an ink stick developed by Kobaien in 1739 and handed down to this day, is widely used throughout Japan. The product is now said to have become synonymous with ink sticks in general.
Ink has long been a necessity not only for monks and government officials, but also for the common people. The history of Kobaien coincides with the history of ink in Japan.
The country’s politics, culture and lifestyle have long been supported by these experienced craftspeople’s skills.
Kobaien has about 200 kinds of products. Kokaboku inksticks range from ¥2,200 to ¥38,500. They are available at stores specializing in calligraphy goods nationwide. It has a branch in Nakagyo Ward, Kyoto.
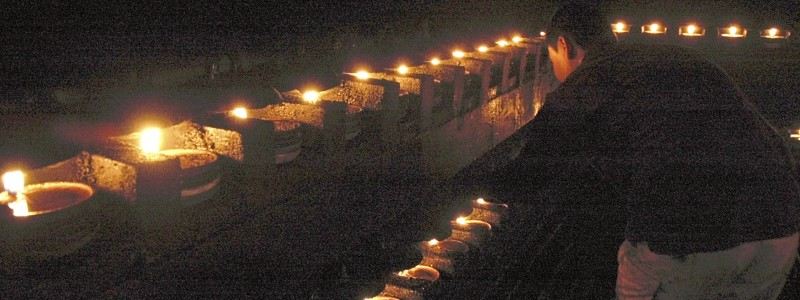
Flames burn in a storehouse of Kobaien to collect the soot.
***
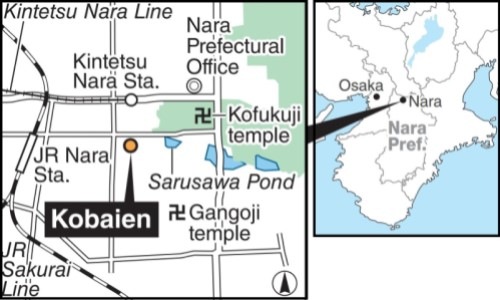
"Features" POPULAR ARTICLE
-
Tokyo Meiji-era Station Bustles with Life Once More; Former Station Remodeled into Commercial Facility, Observation Deck to Watch Passing Trains Up Close
-
Colorful Summer Has Arrived; More than 1 Mil. Visitors Expected to Visit Shonan Hiratsuka Tanabata Festival
-
I Feel Resentment Toward My son’s Wife for Going Abroad on a Working Holiday
-
Wonder of Freezing Foods; Serving Sweets, Snacks Frozen Gain Popularity in Japan
-
My Co-Worker with a Child is Often Absent, Leaves Early
JN ACCESS RANKING