Wood-carver Brings Intricate Shapes to Life
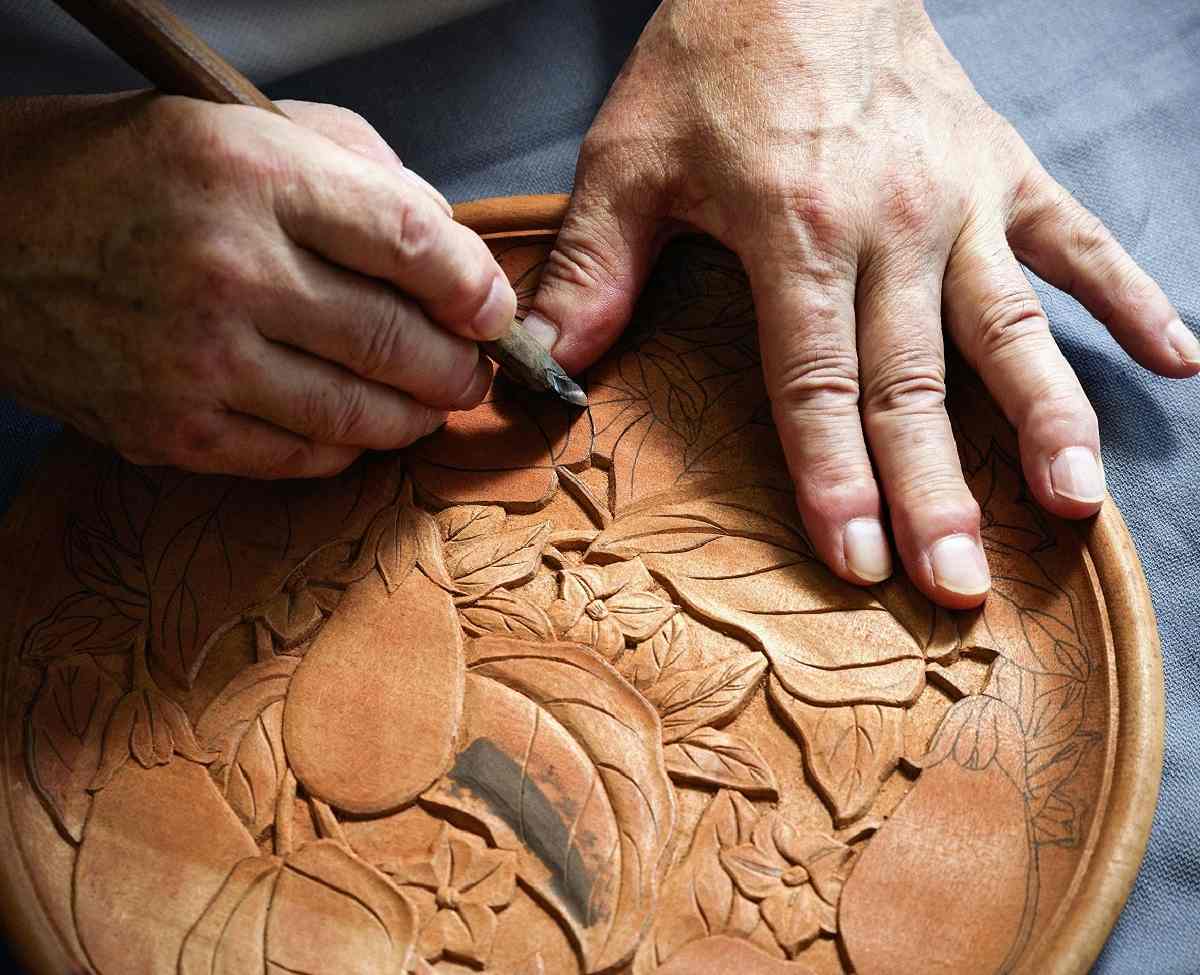
An image is carved into a wooden plate during a process called tachikomi.
13:00 JST, December 3, 2023
KAMAKURA, Kanagawa — Kamakura-bori woodwork artisan Kazuhiko Mitsuki is deeply focused as he carves an image into a wooden plate using a small knife.
“The angle of the knife determines how much depth the image will have and how three-dimensional it will appear,” the artisan said.
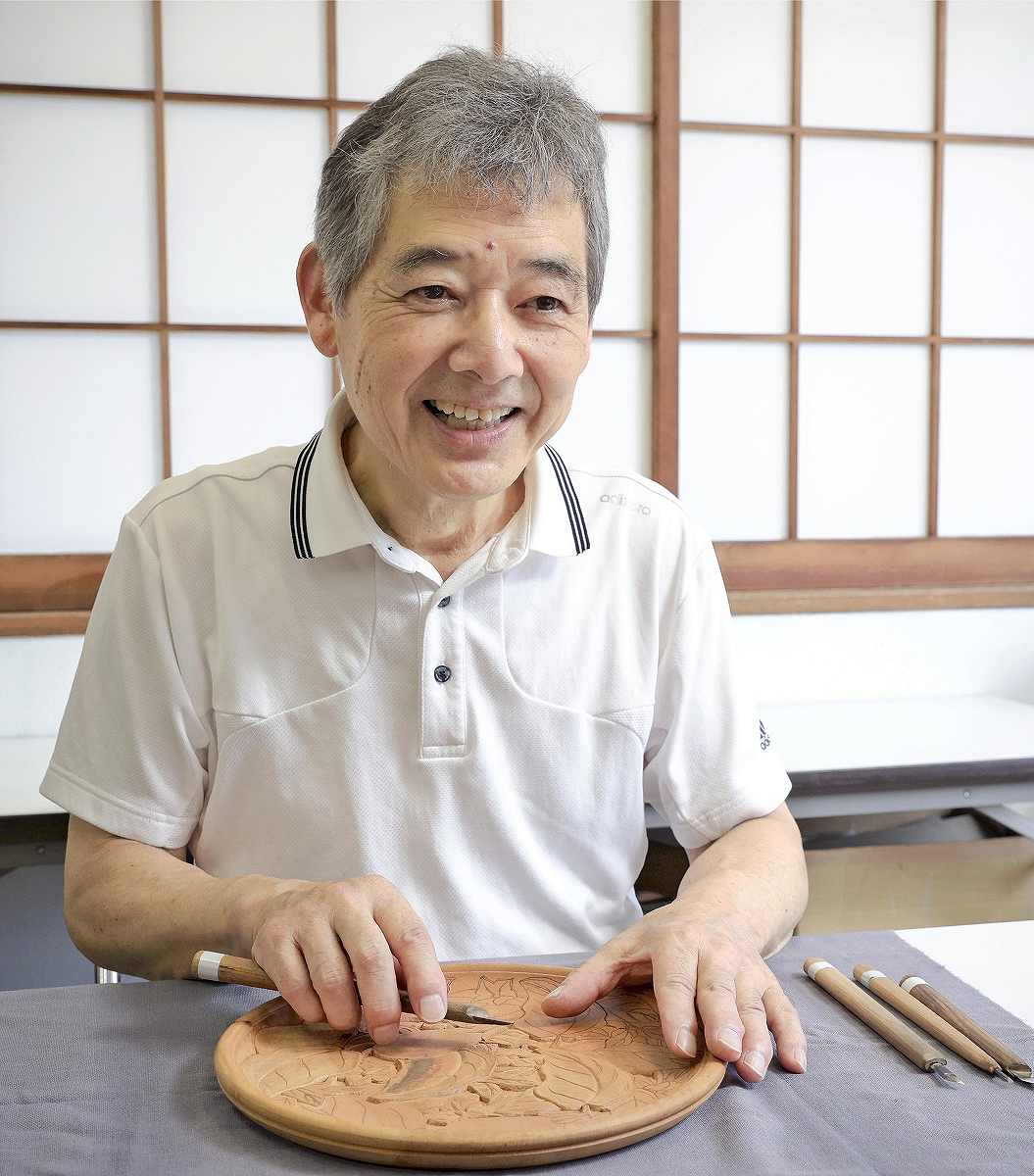
Kazuhiko Mitsuki
Mitsuki, 72, who has more than 40 years of experience under his belt, demonstrated his process. On a wooden plate measuring about 27 centimeters in diameter, Mitsuki began the process of tachikomi, one of the initial steps of Kamakura-bori woodcarving. His knife carefully followed the outline of one of several eggplants, slowly carving out its image. The plate will then be coated with lacquer, dried and polished. The process will be repeated several times.
There are more than 30 steps to his process, so it takes him more than a month to complete one work.
Kamakura-bori is characterized by its rich, dark red color that is achieved through many coats of lacquer. In 1979, Kamakura-bori was designated as a traditional craft.
The technique is said to date back to the Kamakura period (late 12th century to 1333) when Buddhist sculptors, or busshi — influenced by the Chinese tradition of carving elaborate patterns and using many coats of lacquer — carved Buddhist alter fittings.
Temples went into decline during the Meiji era (1868-1912) when the government issued an order to separate Shintoism and Buddhism. During this time, busshi made money by making daily necessities or souvenirs, such as bon and zen trays, plates, bowls, chopsticks and jubako, or tiered lacquerware boxes meant to carry food.
Mitsuki, an Osaka Prefecture native, quit his job at a civil engineering firm when he was 25 and began his career as a Kamakura-bori carver. He said he felt a limit to what he could do at the company as computers began to be used to design bridges and other structures.
Mitsuki said he became interested in the craft after reading a Jiro Nitta novel in which one of the main characters is a Kamakura-bori woodworker.
The artisan often incorporates geometric patterns such as kikkomon, a hexagonal pattern named for its resemblance to a turtle shell, into his designs.
“[The reason I use geometric patterns] might be because I used to create engineering drawings,” Mitsuki said. “One of my old colleagues also pointed that out.”
“Thinking about what materials will be mixed into the lacquer is also fun,” he added. “But more than anything, I like the feeling of making something with my hands.”
Since becoming the president of the Dento Kamakura-bori Jigyo Kyodo Kumiai, a cooperative association of Kamakura-bori businesses, in 2015, Mitsuki has been leading the efforts to promote Kamakura-bori.
He said the industry is currently facing difficulties. At its peak, there were 500 Kamakura-bori artists, and now, there are just over 100.
However, he said the industry will still be able to do well if they can incorporate new ideas and feelings into the works.
The demand for large orders of Kamakura-bori products has decreased, but Mitsuki intends to increase the number of people who enjoy and use Kamakura-bori works through interesting and unique creations. He believes his latest mission is to create an environment in which his successors will feel free to carve whatever they want while respecting tradition.
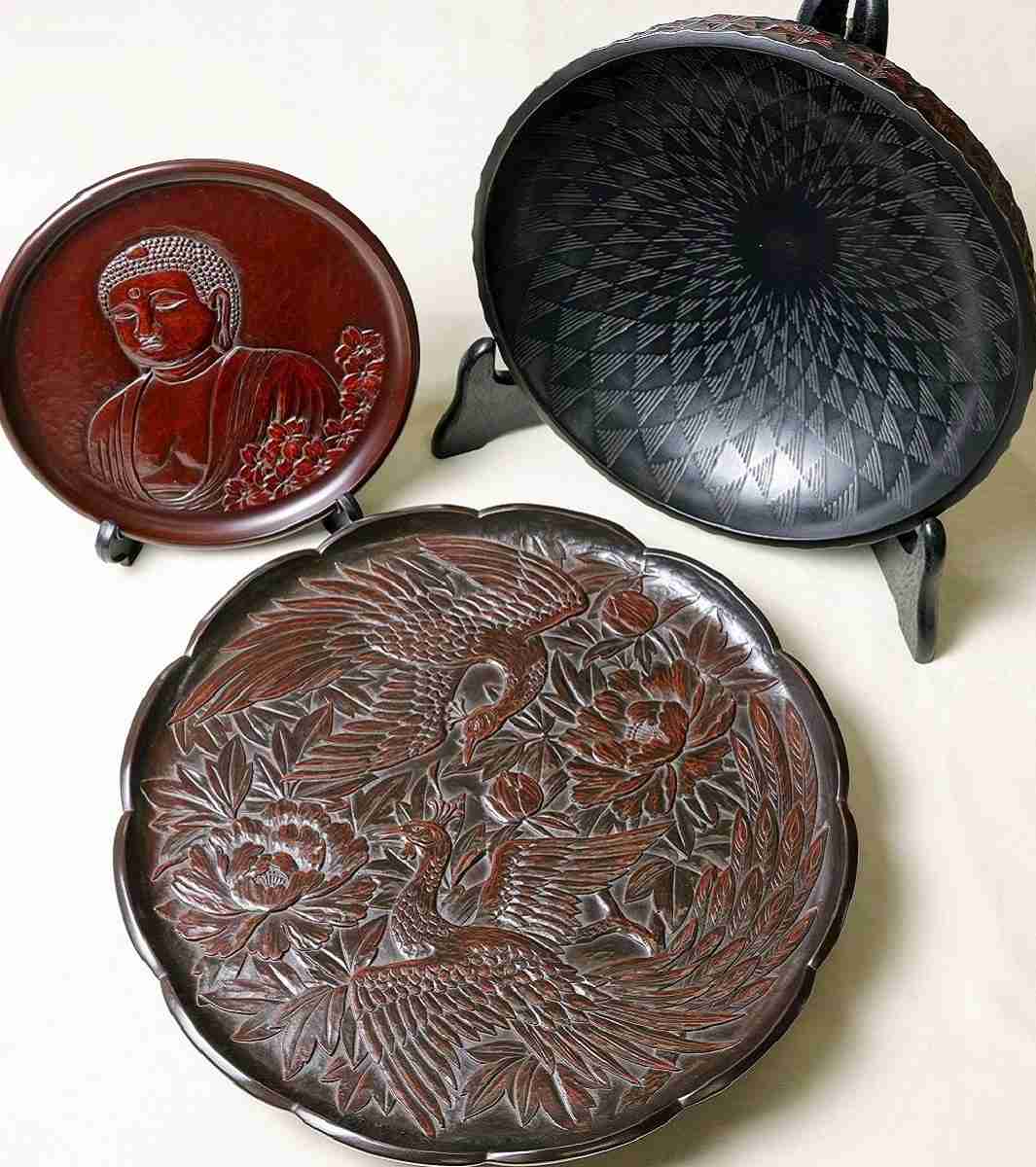
Kamakura-bori works made by Kazuhiko Mitsuki
"Culture" POPULAR ARTICLE
-
Night Parade of Dinosaurs in Tokyo; Lifelike Dinosaurs to Stomp Their Way Through Tokyo National Museum
-
Ueshima Museum, A New Center For Contemporary Art, Opens In Tokyo; Displays Works By Present-Day Artists From Japan And Overseas
-
Art Museums in Japan’s Kansai Region Reopen After Renovations; Many Structures Need Work to Keep Up with Modern Times
-
Indispensable Craftsmanship for Producing Traditional Nara Sumi Inksticks; Going from Doughy Soot to Beautiful Ink
-
Bunraku Plays with Animated Backgrounds to Go on U.S. Tour; Featuring 9 Shows in 5 Cities
JN ACCESS RANKING