Global Shortage of Semiconductors Weighs Heavy on Economic Recovery
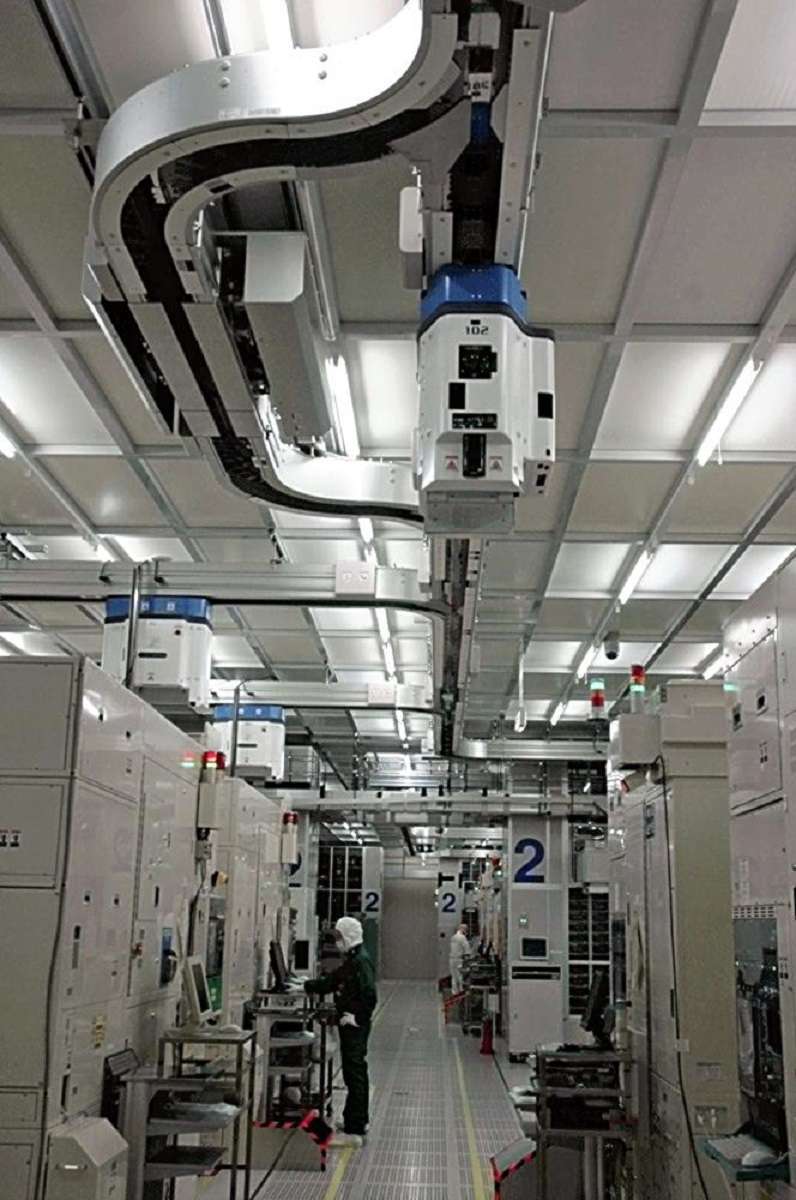
Employees work in a Renesas Electronics plant in Hitachinaka, Ibaraki Prefecture, which is scheduled to increase its production of semiconductors.
14:07 JST, February 28, 2021
The global shortage of semiconductors has become a cause for concern that could impede the recovery of economies already reeling from the novel coronavirus pandemic. A sharp spike in demand for the chips, essential components in smartphones and automobiles, has exacerbated systemic supply chain issues; with production dominated by a limited number of manufacturers, particularly those in Taiwan, the shortage looks poised to become another protracted new normal.
Auto production curtailed
French automaker Renault SA said that the semiconductor shortage, which it expects to peak from April through June, could adversely affect production of 100,000 vehicles, or about 3% of its yearly output. In an earnings call on Feb. 19, Luca de Meo, Renault’s CEO, said that 2021 will be “yet another difficult year,” as the company grapples with a “low level of visibility” on demand and chip supply, backgrounded by European lockdowns and curfews.
The shortage came at a time when leading automakers, including Toyota Motor Corp. and Volkswagen AG, had been ramping up output in response to a rebound in new vehicle sales. But from the start of this year, these same automakers have been forced to slam on the brakes and reduce production around the world. Mitsubishi UFJ Morgan Stanley Securities Co. estimates that the cutbacks will be on the scale of 1.5 million vehicles globally for the first half of this year, from January to June.
Ripple effects of the semiconductor shortage have been felt beyond the automobile industry. The PlayStation 5, a home video game console developed by Sony, can still only be purchased through a pre-order lottery system, over three months after the console was released in November last year. Hiroki Totoki, executive deputy president and CFO of Sony Corp., said at an online press conference on Feb. 3 that “It would be difficult to increase [production] capacity any further.”
Supply chain bottlenecks
Semiconductor demand skyrocketed with the widespread roll out of base stations for the ultrafast, broadband 5G wireless communication network and data center servers. Although the appearance of the novel coronavirus quelled demand for a time, as the pandemic dragged on, lockdowns and social-distancing measures stimulated PC and smartphone sales, and the market for auto part semiconductors rallied in the autumn.
Renesas Electronics Corp., a leading automotive semiconductor maker, plans to step up investment in manufacturing plants and equipment to boost output. According to Renesas president and CEO Hidetoshi Shibata, “The demand [for semiconductors], not only for automobiles but on the whole, has been moving in a bullish trend.”
The semiconductor sector is a classic equipment-intensive process industry, which requires colossal investment in order to stay ahead of the competition. As a result, there are only a handful of companies that are competitive on the global stage. In practice, the actual production of most of the global semiconductor supply is outsourced to subcontractors, particularly those in Taiwan, South Korea, and China, who assemble the chips based on designs from “fabless” semiconductor firms.
Amid escalating trade friction, U.S. sanctions placed on China have in turn flooded Taiwanese manufacturers with even more orders.
As automobile-related business accounts for only around 10% of the total semiconductor market, microchip makers tend to prioritize their supply chains oriented toward PCs and smartphones, a predilection that has now been manifested in the shortage of semiconductors for the auto industry.
Executive order
As the global supply of semiconductors dries up, countries around the world have begun to formulate stopgap measures with growing unease, fearing what a domino effect across the auto industry’s wide array of peripheral businesses could mean for the overall economy.
U.S. President Joe Biden on Wednesday signed an executive order to address supply chain vulnerabilities for four key products: semiconductors, batteries for electric vehicles (EVs), rare earths and pharmaceuticals. The executive order aims to lessen the United States’ dependence on countries such as China while fostering greater cooperation with allies to rebuild supply chains for the stable procurement of critical goods.
Japan, the United States, and Germany have all also taken the unusual step of requesting that Taiwan speed up production of semiconductors for automobiles.
In late January, Taiwan’s Ministry of Economic Affairs brought together its major semiconductor makers — including Taiwan Semiconductor Manufacturing Co. (TSMC), one of the world’s leading semiconductor foundries — and urged them to boost output. TSMC later issued a statement pledging to tackle the auto chip shortage as its “top-priority issue.”
Expanding production lines, however, will require several months. As an analyst cautioned, “it might take anywhere from half a year up to nearly a year” to alleviate the shortage.
High costs sink Japanese makers
Semiconductors have been likened to kernels of “industrial rice” (“sangyo no kome”) in Japan, which is to say, one of the staple bread and butter products supporting Japanese industry. Versatile in application, semiconductors are all around us, providing computational brainpower in the CPUs of computers and phones, storing data in memory cards, and processing images in integrated circuits. A gasoline car typically uses 30 to 40 semiconductors, and electric vehicles require even more.
The global semiconductor market is expected to grow from about $335.8 billion (¥35 trillion) in 2014 to $469.4 billion in 2021.
Up until the latter half of the 1980s, Japanese makers, including NEC Corp. and Hitachi, Ltd., led the global market. But since the 2000s, an increasing emphasis on corporate efficiency split the industry into two camps: namely, the fabless manufacturers such as Intel Corp. of the United States, which primarily handle chip development and design, and the foundries contracted to do the physical manufacturing of the chips.
The Japanese companies that had a hand in both development and production were backed into a corner from a cost perspective, and eventually lost their footing, slipping in the global market standings. Despite repeated attempts at institutional reorganization, these domestic manufacturers have failed to recapture their international competitiveness and continue to fall even further behind their overseas rivals.
"Business" POPULAR ARTICLE
-
Aviation Fuel Shortage Causes Problems at Regional Airports; Growing Demand, Lack of Workers to Transport
-
Prices of over 10,000 Food and Beverage Items to Rise This Year; Figure is down from over 30,000 Last Year
-
Sony Group to End Production of Blu-ray Discs; Market Has Shrunk Due To Growth Of Hard Disk Drives, Streaming
-
AI-Equipped Energy Efficient Air Conditioners Grow In Popularity; Some Can Guess Users’ Moods, Automatically Adjust Temperature
-
Toyota to Introduce 4-Day Workweek for Some Employees; Company Hopes More Flexible Schedules Will Boost Worker Motivation
JN ACCESS RANKING